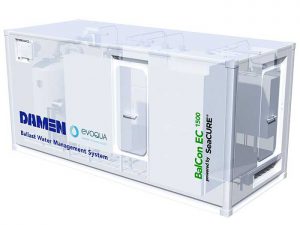
Damen and Evoqua launch “plug and play” BWMS
AUGUST 29, 2016 — Damen Green Solutions and Evoqua Water Technologies will launch a containerized “plug and play” ballast water management system (BWMS) at next month’s SMM event in Hamburg, Germany. The
AUGUST 29, 2016 — Damen Green Solutions and Evoqua Water Technologies will launch a containerized “plug and play” ballast water management system (BWMS) at next month’s SMM event in Hamburg, Germany. The
AUGUST 16, 2016 — Over 60 manufacturers of ballast water management systems (BWTS) with foreign type-approved are now pursing U.S. type approval by utilizing Coast Guard accepted labs to test their systems
To lay-up a vessel means to stop using it for a certain period. It will simply be anchored in appropriate waters or a berth for a few weeks or even a couple of years. The reasons for the lay-up might be to postpone over-capacity or to wait for a better scrap price before selling it. However, lay-up costs need to be taken into account, too.
For example, a six-month lay-up of a Capesize bulker in Malaysia’s Labuan costs between $1,000 and $2,000 per day— far less than the cost of operation which hovers around $7,000 a day, but an investment, because the longer the vessel is in lay-up the higher scrap steel or charter prices have to rise.
Scrapping a vessel means selling it to a ship-breaking yard where workers will cut it to pieces and recycle the steel and other metals, chemicals, and equipment. The owner will receive a price based on the total light displacement ton (LDT) of scrap metal the vessel contains; equipment is taken into account, too.
The market demand defines the LDT price, which is at its lowest in many years. Just recently buyers were offering $270/LDT (as of May 2016), a year ago Capesize bulkers could easily fetch $100/LDT more, and two years ago the figure was $200/LDT more.
Can higher LDT prices be expected? Well, the number of bulkers sold for scrapping is expected to rise throughout 2016 (according to Peter Sand, BIMCO)—this is strengthening the supply. Furthermore, in Asia demand for steel is currently low.
How to lay-up a ship?
Just as the lay-up time can vary, the treatment of vessels varies too, and so do obligations and requirements assigned by class, flag state and port authorities. In general, all responsible parties should be informed. For example, some insurance companies may accept a payment hiatus if the vessel is in lay-up for more than 30 days.
The operator must first decide on either a hot or a cold lay-up. In a hot lay-up condition the ship engines and machinery keep running so that the re-commissioning of the vessel can be carried out very quickly, allowing a cheap and easy vessel preservation. However, with long-term low charter rates in mind, many opt for a cold lay-up, which has lower operational and crew costs, and requires less consumables.
In a cold lay-up vessels are only supplied with emergency energy for lights, windlass/mooring winches and fire extinguishing—often by portable generators installed on deck. Depending on the length of lay-up, three weeks or more should be expected for re-commissioning. Should the lay-up be five years or longer then the re-commissioning time is unpredictable and can last months. The main concern here is protection against humidity, leakage of chemicals and condition of the hull (sea chest/sea water lines).
A dehumidifier has to be installed and connected to the engine room; other items to keep in mind are sea-water tanks, ballast tanks and bow thruster rooms.
Classes, Flag States and Port Authorities
Many classes and port authorities expect minimum manning levels during cold lay-ups to cover at least fire, leakage, mooring and security watch. However, the Safe Manning Certificate applies only to vessels in operation or while vessels are safely at anchor, within port limits or alongside. Requirements of flag states and port authorities apply to laid-up vessels. Flag states in general require notification of vessels laid-up for longer periods—the requirements vary from short notification to a detailed lay-up plan.
In addition, during the lay-up class surveys might take place. For example, DNVGL may carry out an annual lay-up survey (covering watertight integrity, bilge system, fire hazards and equipment in use). After lay-up a number of surveys have to be carried out and expired certificates need to be renewed. Some class authorities require a sea trial when the vessel has been laid up for 12 months or longer.
Green ship breaking?
It seems more environmentally friendly to take old ships out of service than to lay them up for later usage, especially as many were built in times when speed was more important than HFO efficiency.
Indeed, ship breaking can be environmental friendly; approximately 85% of a vessel can be recycled – even the furniture and carpets are sold at local markets in Bangladesh and India. However, the problem is that many shipyards do not handle hazardous chemicals as they should, and consequently the lives of workers are endangered. Rising public awareness has prompted the involvement of authorities leading to the Hong Kong Convention and EU Ship Recycling Regulation. Only time will tell whether these efforts will actually improve environmental and working conditions.
Some yards in China, Turkey and India/Bangladesh are already pre-approved and comply with the Hong Kong Convention and/or the EU Ship Recycling Regulation. However, green recycling often only happens on paper. In this respect the , “Ship Breaking Platform” should be considered, as it does not recognize any yard in India to be green and claims it to be a marketing coup.
Conversely some yards in Europe are recognized even by the NGO as environmentally friendly. For example, Fornaes in Denmark cooperates with the Ship Breaking Platform. Keld Kokholm, Manager of Fornaes, explains: “In general, the offered price per LDT is lower than that which non-environmentally friendly yards in Asia offer due to the expensive recycling of toxic substances and higher labor costs. Furthermore, we and some other European yards are sometimes limited by the size of vessel that we can handle. For example can we recycle ships up to 10,000 tonnes GT or 25 meters in width.” Fornaes therefore focuses on local offshore and fishing ships.
Other companies involved in green ship recycling like Grieg Green AS, can handle big vessels. Grieg Green approves yards based on a list of factors including the safety of workers and downstream waste management, all influenced by the HKC and EU regulation. Here, too, responsible acting results in a current price difference of $70 – $90 per LDT. As stated by Magnus Hammerstad, Area Manager of Grieg Green, this figure is volatile and is related to the local scrap steel price.
Why go green?
Companies which plan to maximize their profit will sell their vessel to a so called cash buyer (a ship broker) who in turn will beach it somewhere in Bangladesh, India or Pakistan. This way the original ship owners avoid regulations and legal trouble.
Recently Maersk opted to recycle the Maersk Wyoming and the Maersk Georgia in a ship-breaking yard in Alang, India which is not on the EU list of green ship breaking yards. Maersk stated that it expects to generate an additional $1 million to $2 million per ship by beaching there.
“Without a strict legal framework and financial mechanism, there are very few incentives for ship owners to choose clean and safe recycling,” said Patrizia Heidegger, Executive Director of the Ship Breaking Platform. “Currently, at the EU level we are debating a ship breaking license, and a financial incentive for clean and safe recycling.”
She pointed out that in addition to new regulations, an increasing number of cargo owners as well as ship financers are demanding ship-recycling policies from ship owners. In the future ship owners may lose both financers and clients if they continue to use substandard shipbreaking.
KLP, the largest Norwegian pension fund, published a report on the human rights and environmental risks related to the current practice of ship breaking.
KLP CEO Håvard Gulbrandsen, states in the report’s foreword: “We hope that the report can help raise awareness of the severe human and environmental risks beaching can entail for shipping industry companies, their customers, and also for other investors […]”.
AUGUST 10, 2016 — Although Damen’s InvaSave mobile ballast water treatment technology is designed for use in ports, in order to qualify for IMO Type Approval the system has now completed shipboard
Marine Log: Tell us about the history of The Pasha Group
George Pasha IV: The Pasha Group is a family-owned, third-generation diversified global logistics and transportation company. My grandfather, George W. Pasha, II, known to many as “Senior,” founded the company in his second career. He was an automotive engineer and worked for distributors of the early classic cars such as Duisenberg, Cord and Velie, selling and servicing their products. He purchased a “Flying A” service station across the street from Fort Mason in San Francisco in December 1941, five days after the attack on Pearl Harbor. The station was an immediate success mainly due to my grandfather’s reputation as an excellent mechanic.
A year later, Senior expanded his operations to provide storage for privately owned vehicles of World War II personnel assigned overseas. This eventually led to the 1947 incorporation of the first Pasha business, Pasha Overseas Automobile Processing Company.
Over the next 20 years, the company grew, especially when George W. Pasha, III (my dad) joined his father and established the first independent automotive port processing terminal on the West Coast at Fort Mason and a body shop on Fisherman’s Wharf to service, repair, and provide a “showroom ready” product. Inheriting his father’s keen business sense, “George III” expanded the company over the years by establishing state-of-the-art automobile facilities up and down the West Coast and in the mid-Atlantic. Today, we market automotive processing services at the Ports of Grays Harbor, WA; San Francisco and San Diego, CA; Baltimore, MD; and Manatee, FL. Our facility in National City Marine Terminal opened in 1990 and has processed over 5 million vehicles to date.
My dad formed a stevedoring and trucking company alongside the auto terminal business to create a comprehensive logistics solution from unloading of inbound vessels to delivery to dealers. In 1972, Pasha Maritime Services was formed and the stevedoring business diversified, adding break-bulk and general cargoes of all types to the service offering. In 1987, Pasha opened an omni-terminal at berths 174-181 in the Port of Los Angeles to provide stevedoring and terminal services of steel products including steel slab. The local company was renamed Pasha Stevedoring & Terminals, as it’s known today.
In the 80’s, the company diversified in the domestic and international logistics business and Non-Vessel Ocean Common Carrier businesses largely through acquisition. One such acquisition was AFI Worldwide Forwarders, one of the pioneering forwarders serving the household goods moving requirements for the U.S. Department of Defense. This expansion brought the company to many corners of the globe.
Both my grandfather and dad had an affinity for Hawaii. My grandfather arranged shipment of military members’ privately owned vehicles to and from Hawaii out of San Francisco. In the 90’s, the company arranged for shipment of new cars for several of our OEM clients. In 1999, the company formed Pasha Hawaii and commenced ocean service between the Mainland and Hawaii in 2005, introducing the first Jones Act-qualified, modern pure car/truck carrier to the domestic trades. The MV Jean Anne, named after my grandmother on my dad’s side, has ably served the market providing efficient carriage of autos, trucks, buses and rolling stock of all shapes and sizes including Stryker tactical wheeled vehicles, rail cars, and construction material and equipment.
In 2015, we welcomed the MV Marjorie C, a combination container/roll-on/roll-off (ConRo) vessel. The Marjorie C, named after my grandmother on my mom’s side, is the only one of its type to ply the Mainland/Hawaii trade lane. The 26,000-ton vessel was engineered from a proven design by Grimaldi in Croatia at Uljanik Shipyard and is the largest ever built at VT Halter in Pascagoula, Mississippi. Pasha Hawaii added Marjorie C to not only offer increased Ro/Ro service to existing customers, but to diversify our service offering by expanding our container capabilities and frequency of service.
Quickly following the introduction of the Marjorie C into the Mainland/Hawaii trade, The Pasha Group also expanded operations via the acquisition of Horizon Lines’ Hawaii business units, and welcomed team members from Horizon Lines and subsidiaries Hawaii-based Hawaii Stevedores, Inc. and the California-based operations of Sea-Logix, LLC. In addition to adding four U.S.-flag, Jones Act containerships, the growth in overall scale and associates supporting these Hawaii business units resulted in a nearly doubling in size of The Pasha Group.
This month, Pasha Hawaii is enhancing service for both container and Ro/Ro cargo from the West Coast to Hawaii Island, with the addition of the Marjorie C providing direct service from Los Angeles to Hilo.
This new route complements the Jean Anne’s current bi-weekly service from San Diego to Hilo. By recently deploying all four container ships to service our LA-Hawaii Express (LHX) and CA-Hawaii Express (CHX) routes, we were able to adjust Marjorie C’s route to include a fast, reliable, 5-day direct call from Los Angeles to Hilo and bring weekly roll-on/roll-off service to Hawaii Island.
ML: How did you get started in the marine business?
GP: I was always fascinated and proud of the business my grandfather founded and my dad diversified and built. I spent summers working for the company gaining experience in all of our divisions. After I received my Economics degree from the School of Business at Santa Clara University, I entered the world of finance, joining Wells Fargo Bank’s training program with the intent of pursuing a career in international banking.
The 80’s were a period of rapid growth and my dad asked me to join him and manage part of our forwarding and logistics divisions. To be able to support my dad in his endeavors was very rewarding. As the oldest of five children, I’ve always felt a great responsibility to both my family and the company. Together my dad and I successfully expanded the scale and breadth of the company. In 2008, I was appointed CEO and assumed responsibility for all divisions of the company, still working very closely with our Chairman, George III.
ML: Tell us about The Pasha Group shipping and logistics business model. How has it evolved over the years since your business first started in 1947?
GP: Growth has been strategic and measured with the goal of having the infrastructure, resources, and capabilities to become a world leader in diversified global logistics and transportation services. Growth and diversification has been largely organic, endeavoring to realize synergies between the divisions and staying close to what we understand and do well. Great effort has been made to stay true to our family values, and through them we strive to support a highly performing group of professionals whose mission is to deliver excellence to a broad base of world-class clients.
The model for many years was asset light. People and property leases in strategic locations were our most important assets. In an effort to allow the company to remain relevant and competitive for another generation or more, beginning with the construction of the MV Jean Anne, we have become a very capital intense business. In 2015, we invested more than $350 Million in our business – a large departure from asset light. However, our newest vessel, the Hawaii assets of Horizon Lines and other transportation assets are all very complementary to the core business. We have leveraged off of the existing organization and internal competencies while complementing with the experienced management, operators and sales folks that joined us from Horizon.
ML: Last year, Pasha added the Marjorie C. Have you been pleased with the performance of the new vessel? Do you have plans to add additional RO/RO vehicle carriers?
GP: Marjorie C has proven to be a great fit for the Hawaii trade. The ConRo vessel has improved our service capabilities through increased capacity and frequency for autos and oversize cargoes as planned. With her unique design, she offers great flexibility by serving a dual role of providing container service while simultaneously serving our Ro/Ro customers. We have also been able to directly call the neighbor islands. Marjorie C features the latest in fuel and emission savings including a shaft generator which uses excess power from the main engine to support electrical needs together with powering of reefer containers.
We are currently actively engaged with the U.S. shipyards to develop our vessel investment strategy. The strategy will balance the needs of the trade, Pasha’s strengths and the opportunity to embrace the latest technologies to assure efficient carriage of goods between Hawaii and the mainland.
ML: Last year, Pasha acquired the Hawaii operations of Horizon Lines. What assets and personnel did that involve and how has the integration of those assets been progressing?
GP: Pasha acquired nearly 900 California and Hawaii-based team members that supported Horizon’s Hawaii business, as well as its subsidiaries Hawaii Stevedores, Inc. (HSI) and Sea-Logix, LLC. In addition, we formed a Dallas service center and brought more than 30 ex-Horizon professionals aboard in that office.
Pasha now owns four former Horizon U.S.-flag container ships (Spirit, Reliance, Pacific and Enterprise) operating alongside Jean Anne and Marjorie C. This provides our customers with increased cargo capacity and the widest range of ocean transportation services between Hawaii and the Mainland. We also expanded our ports to include Los Angeles and Oakland, and more than doubled the frequency of our sailings.
HSI provides us with our own experienced manpower to load and offload cargo in Hawaii, and with Sea-Logix, we now have our own container trucking fleet to pick up and deliver our customers’ cargo, as well as provide trucking to other companies. Adding these businesses has strengthened our integrated shipping and logistics offering to our customers and leveraged synergies within The Pasha Group as a whole.
It’s been a year since the acquisition and the integration of our new employees and assets. The transition has progressed very well. Our success with this very large and complex transaction is due to the dedication of our employees, both current and former Horizon personnel, all of whom share Pasha’s key core values of teamwork, innovation and excellence.
Combining the two businesses allowed us to more effectively serve our expanding customer base while maintaining our customer service philosophy.
ML: Operators are under tremendous environmental regulatory pressure. How has Pasha addressed the issues of emissions, ballast water treatment and sustainability in its operations?
GP: Environmental management is one of the key responsibilities of our in-house Performance Management Team. Route planning, heat balance, hull resistance, and engine performance are just a few of the parameters regularly analyzed to ensure optimum performance on all of our vessels. We currently have projects underway to install stack analyzers and automatic engine tuning to further increase our fuel efficiency and reduce emissions. Through our Ship Energy Efficiency Management Plan we provide the most up-to-date guidelines to our crews for energy conservation.
We are in discussions with Ballast Water Treatment manufacturers and have completed engineering reviews. Currently there is not a USCG approved unit available. When approved systems become available we are prepared. Currently we minimize all ballast water exchange.
Environmental sustainability is important to Pasha and we support long-term ecological balance. We are studying alternative fuels with less environmental impact such as liquefied natural gas. The use of reusable or recycled products is encouraged.
To help eliminate pollution from port-related operations, we are also very proud to announce recently that our Pasha Stevedoring & Terminals L.P. team at the Port of Los Angeles is partnering with the Port to launch the Green Omni Terminal Demonstration Project, a full-scale, real-time demonstration of zero and near-zero emission technologies at a working marine terminal. At full build out, Pasha will be the world’s first marine terminal able to generate all of its energy needs from renewable sources.
ML: What do you see for the future of Pasha? What lessons could you impart to other operators regarding best practices?
GP: The next several years will entail filling in our organization to bring our standard as close to excellence as we can. Meanwhile we will focus on fundamentals of continuing to invest across the company in a balanced way that will promote health and growth across all of our divisions.
The use of ballast water is critical to the safe operation of ships, but also poses challenges due to the need to maintain the structural integrity of ballast water tanks (BWTs) despite highly corrosive conditions. Appropriate protective coatings act as barriers to corrosion and if applied carefully to properly prepared surfaces can significantly extend the life of BWTs. Two-coat epoxy systems are commonly used today, but rapid curing polyurethanes have performance properties that make them attractive as alternative coating solutions, including tunable properties that allow the formulation of flexible yet hard coatings that resist cracking, excellent adherence to steel, high resistance to corrosion, chemicals, and abrasion and fast return to service.
Ballast tanks located at the bottom, around cargo holds, and near the bow and stern of ships provide a mechanism for maintaining balance. Water is filled or released from the tanks to stabilize and trim ships during sailing and to keep them evenly afloat during the loading and unloading of cargo. Ballast water tanks (BWTs) are typically dedicated for this purpose. Ballast tanks are also used to adjust the buoyancy of submarines and stabilize offshore oil platforms and floating wind turbines.
In marine vessels (tankers, bulk carriers, etc.), ballast tanks typically comprise the largest surface area of steel. Corrosion of these tanks can therefore significantly reduce ship safety and operational life. In the past, ships suffering from severely corroded ballast tanks have experienced total failure of their hull shell plates. There is general agreement in the industry that prevention of corrosion in BWTs is the second most important factor after design integrity in determining the operating life of a ship.
Corrosion prevention in BWTs is not a simple matter, however. The water in ballast tanks can have a high salt content, vary in the type and concentration of other ions and have a wide range for pH and may also contain corrosive chemicals. Empty ballast tanks, on the other hand, are exposed to corrosive atmospheres that cycle with the temperature of the tank. Tanks, when partially full, are also subject to continuous movement of the water.
In fact, different parts of ballast tanks corrode via different mechanisms and at different rates, and empty tanks behave differently than tanks that are often filled with water. For Example, some parts of tanks are exposed to cyclic heating and cooling and/or local heating from warm, adjacent cargo tanks and engine rooms. Additionally, the exterior of the BWT is exposed to the weather above the water line and the differing temperatures of the sea below the water line. Therefore the same tank can experience uneven thermal cycling due to the extreme differences in its exterior exposure. Because the upper portion of the tank is exposed to extreme thermal cycling and repetitive wet and dry service, anodic oxidation is the main source of corrosion in this part of the tank. On the other hand, the bottom area of a tank is constantly exposed to the sea and therefore is maintained at a lower temperature and is subject to cathodic blistering. Any microbes in sediment on the bottom can also cause microbial corrosion.
Many other factors such as bacterial biofilm, mechanical vibration and effectiveness of sacrificial or impressed current anodic protection play a moderate role in determining the rate of corrosion in ballast water tanks.
To prevent corrosion in BWTs, high-performance protective coatings are applied during construction of the ship. Typically two thin layers of a suitable coating with a total dry-film thickness of approximately 300-320 microns are sufficient to provide an effective barrier against corrosion. Such coatings must meet many regulatory requirements related to their environmental and performance characteristics.
Current Coating Technologies
Preferred coatings not only provide a long lifetime of protection (15 years or more is required by the International Maritime Organization (IMO) Performance Standard for Protective Coatings (PSPC)¾see below), they must be easy to apply under the varying conditions found at different shipyards around the world and easy to maintain. Coatings that provide greater coverage for less material usage and are more tolerant of poorer surfaces are also in demand. A low volatile organic compound (VOC) content (< 250 g/l) is also necessary.
The majority of BWT coatings applied today are epoxy-based systems. Most are solvent-based, high solids formulations, although some European shipbuilders use solvent-free coatings to meet the requirements of the EU Solvent Emissions Directive (SED). The latter 100% solids epoxy systems have good performance properties, but tend to suffer from poor wetting properties and slower curing rates at low temperatures. Good wettability is necessary to ensure that pitted areas are filled rather than bridged, and thus do not leave a void below the paint film that can act as a starting point for corrosion.
Rapid curing is a very desirable property for BWT coatings because it translates into shorter construction times for new builds and reduced time in dry-dock for recoating and repair. The US Navy has developed a series of 100% solids coatings based on amino polyols prepared from either alkanol amines and polyfunctional epoxy materials or polyamines and monofunctional epoxides that are applied using plural component equipment, which eliminates the poor flow concerns. They are referred to as “single-coat” systems because the necessary two coats can be applied in one day, rather than in two. The technology for a light-to-medium-duty coating based on a medium-viscosity resin has been licensed and is commercially available. In a study at a commercial shipyard in Asia, the rapid curing coating, which meets the IMO PSPC requirements, was shown to provide a nearly 40% increase in painting productivity and a 20% overall cost savings.
Advantages of Polyurethanes
Certain polyurethane (PU) coatings have also been shown to have significant potential as highly protective barrier coatings for ballast water tanks. Specifically, 100% solids rigid and structural polyurethane coatings are promising because they cure very rapidly, even at cold temperatures, and have superior resistance properties.
One of the major issues with epoxy coatings is their inability to build desired dry film thickness at sharp edges, corners, weld seams and other defect sites. Coating failures generally occur first in these areas, usually do to crack formation. Unfortunately, there are many of these sites present in BTWs. While the PSPC does require that sharp edges be addressed prior to coating, this problem remains a concern in the industry. Advances in epoxy coating technology have helped, but further improvements are still desired.
Polyurethanes have the key advantage of property tunability. Careful selection of the polyisocyanate and polyol segments can provide coatings with very specific properties. For ballast water tank applications, a hard coating is needed that retains some flexibility to allow for high film builds at edges, seams and defect sites. This unique mix of properties, which cannot be achieved with epoxy systems, is possible with polyurethane coatings. Careful preparation of the PU resin and development of the formulated PU coating can provide coatings with desirable edge retention properties.
With the appropriate choice of starting materials, it is also possible to formulate polyurethane systems with curing times that allow for the application of perfectly smooth, high-build coatings. These barrier coatings are applied with no defects in one continuous application and serve as abrasion- and impact-resistant protective barriers to corrosion. Furthermore, because they contain no solvent, 100% solids polyurethane coatings are “green” coatings that meet stringent environmental regulations, and most are odor-free, providing a better shipyard application environment than high-solids epoxies.
Surface adhesion, as for all coating applications, is crucial for BWT coatings and has a significant impact on coating performance. More forgiving coatings that have strong adhesion to the different types of steel used in shipbuilding and the different types of surface conditions that can be present are therefore highly desired for the protection of ballast water tanks. Polyurethanes meet this requirement and generally surpass the adhesion properties of many epoxy systems.
The inherent barrier properties of polyurethane coatings are also excellent. PUs show high resistance to corrosion and chemicals. In addition, they provide superior abrasion and impact resistance, which is not true for epoxies systems. Finally, the very rapid curing of polyurethanes over a wide temperature range makes them suitable for application to water ballast tanks regardless of where they are built or dry-docked and ensures reduced coating times during newbuilding and fast return to service for repair/maintenance operations.
Performance Requirements: PSPC and Invasive Species Control
The IMO PSPC became effective in 2008 and provides specific requirements for the types of corrosion control coatings that can be used on ballast water tanks, as well as appropriate application, inspection and maintenance procedures. Extensive documentation is also specified in the standard. The intent is to have all BWTs coated with systems that will provide a 215-year service life.
Coating systems must be pre-qualified/certified prior to use in ballast water tanks. Certification can be obtained from an approved, independent testing laboratory, through demonstrated performance in the field for a minimum of five years, or by presenting results from previous, relevant tests. Coating application during the newbuilding process must be extensively monitored, and inspections performed at numerous phases. For example, testing of the surface profile and water-soluble salt content are required before application of the first coat, and a thorough inspection of the first coat is necessary before the second coat can be applied. These requirements can slow down the coating process and increase the cost. Consequently, rapid-cure coatings that allow the application of two coatings in a single day are attracting significant attention.
Recent regulations attempting to prevent the spread of invasive species through ballast water must also be considered when installing BWT coatings. There have been several cases of the transport of invasive species around the world, some of which have had severe ecological and/or economic impacts. However, many of the current chemical technologies available for destroying harmful marine organisms in ballast water are based on oxidizing agents (e.g., chlorine dioxide, ozone) that are damaging to the coatings and can lead to corrosion problems. Mechanical systems based on filtration/separation and those that use ultraviolet radiation tend to be less problematic. Therefore, it is crucial that testing of corrosion control coatings for ballast water tanks be performed under maximum treatment conditions for a given application.
A Word about Surface Preparation, Quality Assurance and Maintenance
As with all coatings, surface preparation is critical to the performance of BWT coatings. In fact, lack of proper surface preparation is one of the main causes for coating failures in ballast water tanks. It is imperative that appropriate surface preparation standards (SSPC/NACE/ASTM) be met. Attention should be paid to both surface profile and soluble salt content.
Application conditions must also be considered, as temperature and relative humidity during application can affect the ultimate performance of many coating systems, particularly epoxies. While most large, modern shipyards have enclosed areas for conducting abrasive sand blasting and painting (with temperature and humidity control), some smaller facilities do not. Work is therefore performed under ambient conditions using power tools, which can result in poor surfaces for coating. Polyurethanes offer advantages in these situations, as they have superior adhesion to poor surfaces and temperature and humidity do not impact their curing or ultimate performance properties.
PUs are Good for Potable Water Tanks
The properties of polyurethanes that make them ideal as corrosion protection coatings for ballast water tanks also make them well-suited for use as protective systems for marine potable water tanks. Many polyurethanes meet the requirements of the ANSI (American National Standards Institute)/NSF (National Sanitation Foundation) Standard 61 – Drinking Water System Components, which establishes stringent requirements for the control of leachables and extractables from materials that come in contact with either potable water or products that support the production of potable water.
Conclusion
Preventing corrosion in ballast water tanks is crucial for ensuring the safety and longevity of on marine vessels. While epoxy systems are currently the most common coatings used in this application today, properly formulated, fast-curing polyurethanes are attractive alternatives with significant potential to reduce lengthy coating processes, increase shipyard productivity and thus reduce costs.
JULY 7, 2016 — Sandnes, Norway, headquartered ballast water treatment (BWT) system specialist Optimarin reports that it has successfully completed the U.S. Coast Guard’s (USCG) environmental test and all land-based and shipboard
JUNE 27, 2016 — Chesterfield, U.K., based Cathelco Ltd. has supplied a ballast water treatment (BWT) system for the C.C. Pacifique, a steel barge that is being converted into a cable laying
JUNE 14, 2016 — The 5,400 TEU containership Carl Schulte’s is meeting the most stringent environmental standards so successfully that it is ranked in the top 2% of containerships of its size
MAY 20, 2016—While no ballast water technology manufacturer has yet gained U.S. Coast Guard Type Approval, some are now reporting that they have completed land-based and shipboard testing, the final steps on