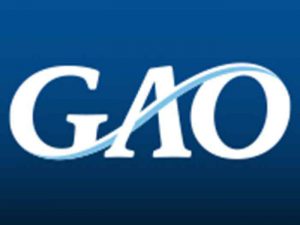
GAO reports on Navy ship repair contracting strategy
NOVEMBER 22, 2016 — In 2015 the U.S. Navy introduced a new contracting strategy for ship repair, called Multiple Award Contract, Multi Order (MAC-MO). A report to Congress by the GAO finds
NOVEMBER 22, 2016 — In 2015 the U.S. Navy introduced a new contracting strategy for ship repair, called Multiple Award Contract, Multi Order (MAC-MO). A report to Congress by the GAO finds
Considered the “forgotten borough” by some New Yorkers, Staten Island is on the verge of making its presence known in the city that never sleeps. The borough is a 25-minute ferry ride from the lowest tip in Manhattan, the Staten Island Ferry terminal at Whitehall.
Staten Island’s plan for renewal includes a $1.2 billion investment that will see the construction of the New York Wheel at St. George—an impressive 630 ft tall observation wheel that will rival England’s infamous London Eye, and feature 36 pods with accommodations for 40 in each, on a 38 minute ride/revolution, giving passengers a spectacular view of New York Harbor. Alongside the New York Wheel, New York City’s first outlet mall, Empire Outlets, is currently being constructed at St. George. The mall will feature 350,000 square feet of retail, 100 different shops and a 190-room hotel. Both the New York Wheel and Empire Outlets are expected to be operational by 2018.
How will tourist, potential shoppers, and New Yorkers alike make their way to these new attractions? They’ll be taking the Staten Island Ferry of course. The fleet, currently comprised of nine ferries, carries 22 million passengers a year—second only to Washington State Ferries’ fleet which carries over 23 million passengers annually.
And come 2019, the Staten Island Ferry fleet will welcome a new class to its fleet—the Ollis Class ferries.
Designed by Seattle-based Elliott Bay Design Group, the Ollis Class will mix the new with a bit of the old, providing passengers with a faster, more efficient ride to help meet increased ridership demand.
Its design will give the 320 ft x 70 ft ferries a striking resemblance to the beloved John F. Kennedy—which was commissioned in 1965 and is one of the oldest ferries in the Staten Island Ferry fleet. The Kennedy is one of three-that will be retired once the new Ollis Class series is delivered—the S.I. Newhouse and Andrew J. Barberi, both commissioned in 1981 are the other two.
The new Ollis Class will be double-ended and have capacity for 4,500 passengers; and like the Kennedy, will feature plenty of open air space, enabling passengers to enjoy the harbor view. The ferries will be built to ABS class requirements and will be powered by Tier 4 EMD engines and Voith Schneider Propulsion Drives.
The first of the three ferries will be named in honor of U.S. Army Staff Sgt. Michael Ollis, a native Staten Islander who died while saving another soldier in Afghanistan. He was only 24 years old.
The Staff Sgt. Michael Ollis ferry is expected to begin operations in 2019, with vessels two and three following later in 2019 and 2020.
Building the Ollis Class
As we were going to press, yards were putting in their final bids for the ferry project.
Among the yards that have expressed interest in the Ollis Class—at least according to the 2015 Industry Day attendance—are Conrad Shipyard, Eastern Shipbuilding Group, Fincantieri Bay Shipbuilding, and Vigor. All are builders of a variety of vessel types including ferries.
Conrad Shipyard—which has won a number of newbuild contracts this year — has had its share of ferry projects in the past, and is looking to keep the momentum going.
As Dan Conrad, Conrad Shipyard’s Senior Vice President and Director, explains, “Conrad Shipyard has a great track record on deliveries to the Puerto Rico Maritime Authority, the Texas Department of Transportation, the State of North Carolina and the Alaska Marine Highway, among others.” And he assures that his team is committed to pursuing the ferry market for years to come.
Most recently, Conrad’s Conrad Aluminum, Amelia, LA, yard delivered the M/V Woodshole to the Steamship Authority. The 235 ft x 64 ft ferry was designed by Elliott Bay Design Group and has capacity for 384 passengers, 55 automobiles or 10 eighteen-wheel tractor-trailers.
Eastern Shipbuilding Group is said to have the inside track on building the Ollis Class ferries, according to our sources. It would be quite a month for the Panama City, FL-based shipyard, which recently secured the lucrative contract to build the OPC for the U.S. Coast Guard.
Meanwhile, Fincantieri’s recent expansion is helping it position its Bay Shipbuilding yard for larger projects that can be produced and worked on, year-round. The three-acre expansion will pave the way for additional covered fabrication and erection facilities, an indoor paint and coating building, and outfitting shop that will enable FBS to increase its pursuit of ferry projects.
“This expansion allows us to increase our capacity and positions us to pursue a number of new construction markets, including large passenger ferries,” said FBS Vice President and General Manager Todd Thayse. “Our experience in building ferries and other complex passenger vessels dates back to our origins almost a hundred years ago, and includes the New York Staten Island Ferry now operating (the Guy V. Molinari). We have the people, the experience, the facilities, and the global resources of Fincantieri to ensure that we can tackle the most challenging construction projects.”
As for the shipbuilding powerhouse in the Northwest, Vigor, it’s currently working on six ferry projects at the moment, including the final two vessels in Washington State Ferries’ new 144-car Olympic Class.
“Vigor has deep expertise in the ferry market with successful, on-time and on-budget deliveries of car ferries, passenger only vessels and catamarans. Six ferries are currently under construction at our Washington and Alaska yards and we expect ferry construction to continue to be a focus in our business development efforts, leveraging our considerable experience,” said Corey Yraguen, Vigor Executive VP of Fabrication.
Just last month the Chimacum, the third in the series was christened at Vigor’s Harbor Island yard. The fourth vessel in the series, the Suquamish, is currently under construction and scheduled for completion in 2018, with operations set to begin in 2019.
The 144-car ferries are the result of a combined effort from a consortium of Northwest based companies, including Nichols Brothers Boat Builders, Freeland, WA, which has been in charge of building the superstructures for the144-car ferries.
In other Vigor ferry news, Vigor’s Ballard Facility (formerly Kvichak Marine) is building two 400 passenger ferries for the Water Emergency Transportation Authority of San Francisco (WETA). The Incat Crowther designed ferries will travel 27 knots and are scheduled for delivery Summer 2017.
And Vigor’s Ketchikan yard in Alaska has taken up the task of constructing the highly anticipated 280 ft Day Boat ferries for the Alaska Marine Highway System. The ferries, designed by Elliott Bay Design Group, are scheduled to be completed Fall 2018.
Vigor’s Executive VP of Business Development, Keith Whittemore, will be discussing Vigor’s ferry projects and more at the Marine Log Ferries Conference & Expo November 3 & 4, 2016, Seattle, WA. Attendees of the event will also have the chance to tour Vigor’s Harbor Island yard after the conference’s conclusion. Learn more at www.marinelog.com/events
Route Extension?
Staten Island Borough President, James Oddo sparked additional interest in the Staten Island Ferry system when he requested the New York City Department of Transportation explore the feasibility of extending the Staten Island Ferry’s route north of the Whitehall Terminal, possibly extending the service into midtown.
While the idea sounds great in theory, and will certainly foster a sense of “transit equality” for Staten Islanders who have a grueling commute (just ask our Editor-in-Chief, John Snyder), the route extension could prove problematic as there is currently no operating terminal in place in midtown, with the right infrastructure to handle such large vessels.
New York’s Ferry Boom
Of course, the Staten Island Ferry isn’t the only New York City ferry operation making waves. Operated by Hornblower NY, Citywide Ferry Service’s new fleet of ferries are currently under construction at Louisiana-based Metal Shark Boats and Alabama’s Horizon Shipbuilding. The contract catapults both yards into new markets—propelling Metal Shark into the commercial market in a very big way, and introducing Horizon to the ferry market.
A large portion of the Incat Crowther-designed ferries are expected to be delivered in time for Citywide Ferry Service’s launch Summer 2017. The service, according to the New York City Economic Development Corporation is projected to make 4.6 million trips annually.
The 85 ft ferries will have capacity for 150 passengers, as well as space for bikes, strollers and wheelchairs. The Citywide Ferry Service is expected to add five new routes on the East River.
Meanwhile, another well-known ferry operator in New York harbor is upping its stake in the market. Seastreak says its “raising the bar in fast passenger ferry service” with the addition of a new, high-speed, 600-passenger, catamaran in 2017. The ferry will be the highest passenger capacity USCG K-class high speed ferry in the U.S.
The addition of the new ferry will help Seastreak meet growing passenger demand on the New Jersey to New York route.
Designed by Incat Crowther, the ferry, the first in Seastreak’s new Commodore class, will be 147 ft 8 in x 39 ft 5 in. The vessel was designed to provide Seastreak with an operational advantage. The ferry’s boarding arrangement will include large forward and aft side gates as well as an adjustable bow ramp. This will help facilitate turnaround times at terminals.
The first vessel in the series will be built at Gulf Craft Shipyard, Franklin, LA. Construction is to be completed by 3rd quarter 2017. Meanwhile, Seastreak expects a keel to be laid for a second Commodore class vessel before the end of 2016.
The Commodore Class ferry will be powered by four MTU 12V4000 M64 EPA Tier III main engines, each delivering 1,875 hp at 1,800 rev/min and driving Rolls-Royce KaMeWa 63S4 waterjets. The vessel will also feature LED lighting and an advance energy efficient HVAC system.
The ferry’s main deck will hold 234- passengers; mid deck will seat 271 passengers inside and 52 passengers outside; and the third deck features 160 exterior seats as well as the vessel’s wheelhouse.
Seastreak is also initiating the upgrades and repowering of several members of its current operating fleet. First one up will be the Seastreak New York, which is expected to enter into drydock this coming winter. At press time, the bids were out to multiple yards. The repowering project is expected to be completed by the end of the 1st quarter 2017.
Florida gets in the game
New York isn’t the only city getting its ferry action on. This month, service officially begins on the Cross-Bay Ferry system—connecting St. Petersburg and Tampa, Fl. The service is part of a pilot project intended to introduce residents and visitors to water transit services in the area.
The route will be operated by the 98 ft twin-hull aluminum catamaran, Provincetown IV. The ferry was originally built for Bay State Cruise Company, Boston, MA, by Gladding-Hearn Shipbuilding, the Duclos Corporation, Somerset, MA. Designed by Incat Crowther, the 149-passenger ferry can operate at a top speed of up to 30 knots on the 50 minute route.
“We only have one vessel, and one crew, so we cannot do everything, but we do mean to showcase this technology to a lot of people and test ferry service in a variety of ways and markets,” said Ed Turanchik, policy advisor for the project.
Organizers of the project are testing the service on a variety of different market segments including tourist and local commuters, and the entertainment and sports markets. Learn more about the project at CrossBayFerry.com.
VDOT accepts ferry bids
Last month, the Virginia Department of Transportation was accepting bids for a new 70-vehicle ferry based on a design by Alion Science. The boat would be a replacement for the VDOT’s oldest ferry, the Virginia, built in 1936. Construction on the steel-hull ferry is to start this fall with completion in 2018.
Gladding Hearn delivers high-speed ferry
Gladding-Hearn Shipbuilding, the Duclos Corporation, recently delivered a new 493 –passenger, high-speed Incat Crowther designed ferry to Hy-Line Cruises, a division of Hyannis Harbor Tours, Inc., Hyannis, MA.
The all-aluminum ferry is 153.5 ft x 35.5 ft and is powered by four Cummins QSK60-M, EPA Tier 3 diesel engines each delivering 2,200 bhp at 1,800 rev/min. Each engine will power a Hamilton HM721 waterjet through a Twin Disc MG61500SC horizontally-offset gearbox.
Incat Crowther says the ferry represents an evolutionary step from its previous designs built by Gladding-Hearn. According to the designer, the capacity increase had to fit within docking constraints, enforcing upper limits on both the length and beam of the vessel. To meet the requirements, it moved the wheelhouse to a third deck, freeing up the front end of the second deck for VIP passengers.
The restructuring shifted boarding arrangements, with the addition of a middeck boarding door and both forward and aft stairways improving passenger flow and turnaround times, says Incat.
The ferry will provide year-round service between Hyannis and Nantucket Island. It will top speeds of over 34 knots when fully loaded at a deadweight of more than 64 tonnes, said Peter Duclos, President of Gladding-Hearn.
The new ferry is also outfitted with a Naiad Dynamic trim-tab, ride-control system to help improve passenger comfort and safety. The system’s motion sensor measures the relative movement of the vessel and transmits a signal to the hydraulic device to counter the boat’s actions through the waves.
Europe’s Ferry Market
The European ferry market remains in the forefront of technology. The continent that gave the world emission-free, battery operated ferries, will now give forth, the world’s largest hybrid ferry.
Just last month, Norway’s Color Line reported that it would order the largest hybrid ferry ever built. The ferry, which will feature batteries charged via green electricity from dedicated shore side facilities, or recharged on onboard via the ship’s generators, would double the capacity of the vessel it will replace.
Tentatively named the “Color Hybrid, the ferry will be 160 m long and have capacity for 2,000 passengers and up to 500 cars. The ferry is expected to be put into service on the Sandefjord, Norway to Stromstad, Sweden route in 2020.
And not to be outdone, Damen says its ready to launch its first composites-construction Water Bus. As we were going to press, the prototype was prepping to begin sea trials.
The Damen Water Bus is the first vessel for public transportation produced at Damen Shipyards, Antalya, Turkey. Its benefits are plentiful—the vessel, which features a slender hull, making it lighter than a traditional aluminum vessel, requires less fuel consumption, less maintenance, will suffer from no corrosion or fatigue problems. It can travel at speeds up to 21 knots and has capacity for 100 passengers.
Damen’s Design & Proposal Engineer, Fast Ferries, Marcel Elenbaas, explains that the Water Bus is built using high quality vacuum infusion technology that creates a “difficult to penetrate closed cell, epoxy sandwich structure.”
Damen says the vessel is ideal for highly congested urban areas, and is a simple and efficient way for using a city’s natural waterways system.
The Water Bus is equipped with two, forward facing, double-screw podded propulsion units—helping to reduce vibrations. Damen says the vessel can be easily adapted to customer specifications, and because of the nature of the composites’ production process, delivery to clients will be quick.
The commercial fishery has been part of the lifeblood of Eastern Canada for more than five centuries. Adjacency to the fishing grounds was the initial catalyst for the settling of the near countless harbors, coves and inlets throughout the five provinces that border the rich, pristine waters of the North Atlantic. And while the technology and vessels used to prosecute the fishery has changed over the generations, the industry in Newfoundland and Labrador, Nova Scotia, New Brunswick, Prince Edward Island and Quebec is more valuable than it has ever been.
The seafood caught and produced in Eastern Canada is now worth nearly $2.4 billion (CDN landed value) annually.
According to the most recent statistics from the federal Department of Fisheries and Oceans (DFO), the value of all seafood produced in the five Eastern Canadian Provinces totals an impressive $2,387,424. This number is quite staggering when you think about it. Few industries in this region produce products that contribute this much to the economy and gross domestic product (GDP) in one year.
As one would expect, a wide variety of species contribute to the overall multi-billion dollar total. But it will come as no surprise to anyone associated with the fishery or seafood industry in Eastern Canada what group or species really drives the industry here — shellfish. This group of crustaceans accounts for an impressive $2.37 billion.
Lobster is king in Eastern Canada, with a value in excess of $942 million and shows no sign of slowing down. Lobster catch rates are increasing year-over-year. Combine this with record prices and you have the formula for a very valuable and sustainable fishery.
Next in order of economic importance is snow crab, contributing $534 million, followed closely by Northern shrimp at $369 million. Scallops round out the top four shellfish species at $178 million.
The seafood industry continues to be a strong employment driver in the region, responsible for more than 50,000 direct jobs – both seasonal and permanent – in the harvesting and processing sectors. This, of course, does not include the thousands of spin-off jobs associated with the fishery and millions of additional dollars pumped back into the Eastern Canadian economy.
While the fishing industry is producing literally billions of dollars in product each year, it is not without its challenges. In fact, few industries in Eastern Canada, if any, have faced the adversity the fishery has over the decades – including dwindling stocks, quota cuts, labor shortages, constant conflicts with the federal government and building competition from outside Canada. Those catching and producing seafood in this region have seen and experienced it all – but have always persevered.
Northern Cod Stocks
The biggest story coming out of the Eastern Canadian fishery as of late involves groundfish stocks – cod in particular.
In 1992 the Federal Government of Canada declared a moratorium on the Northern Cod fishery, which for hundreds of years had largely shaped the lives and communities of Canada’s Eastern coast. After it was discovered in the late 1980s that the Northern cod biomass had fallen to one per cent of its historical levels, the fishery was essentially shut down, ending the region’s 500-year dependence on Northern cod.
But cod is making a comeback.
A 2015 study into the state of Northern cod stocks off Newfoundland and Labrador confirmed a dramatic recovery for a species that became virtually commercially extinct in the 1990s — a confirmation that commercial fishermen have been documenting and commenting on for several years.
The study, co-authored by well-known and respected fisheries scientist George Rose, reported that the cod biomass has increased from tens of thousands of tonnes to more than 200,000 metric tonnes within the last decade and shows signs of continued growth. In fact, Canada’s federal Department of Fisheries and Oceans (DFO) recently reported that according to its research, the spawning stock biomass was actually in the range of 300,000 metric tonnes.
The news of the groundfish recovery has been met with optimism— so much so that DFO just announced in August of this year, the first expanded commercial Northern cod fishery in decades.
Another bright spot for the Eastern Canadian fishing industry is the Comprehensive Economic and Trade Agreement (CETA) between Canada and the European Union. Once ratified in 2017, this free trade agreement will lead to the dropping of the punishing tariffs now applied to Canadian seafood exported to the member states of the EU. Not only will this agreement increase the profitability of Eastern Canadian seafood companies now shipping product overseas, but will open up a vast array of new, hungry markets, with an appetite for fresh, top quality Canadian seafood.
Shipbuilding Resurgence
When any industry is doing well and its participants are prospering, that good fortune has a tendency to spill over to related spin-off and supply companies – and the Eastern Canadian fishing industry is no exception.
One area that has seen a renewed revitalization in recent years is the region’s shipbuilding industry.
Many Eastern Canadian yards, that a decade ago were either shuttered or only producing a few vessels per year, have sprung back to life and are now at capacity – with many booked up to three-four years. New fishing vessels are in demand in Eastern Canada more than ever and the region’s naval architects and builders are just trying to keep up.
Rick Young is witnessing this growth and resurgence in shipbuilding first hand. Young is a Director and Owner of TriNav Marine Design and Marine Services International – two St. John’s, Newfoundland-based companies that design and provide in-depth technical assistance to the Eastern Canada shipbuilding and marine sectors.
“There was considerable vessel construction activity in Newfoundland and Labrador from 1995 to about 2005, mostly related to changes in the industry from harvesting groundfish to harvesting shellfish. Nova Scotia and the other Eastern Canadian provinces have seen a steady growth in vessel construction in the past five years or so due to strong market prices for lobster and also because much of the fleet was getting old and required replacement,” Young said.
He noted that fishermen have lobbied hard over the years and have been successful to have DFO change many of their vessel size restrictions.
“This has allowed fishermen to construct larger and safer vessels that can travel further offshore for longer periods of time, while increasing quality with such features as live wells and refrigerated sea water tanks.”
Now with the potential for a renewed groundfish fishery in the near future and continued strong prices for shellfish, fishermen are willing to invest further in newer and multi-purpose vessels, Young added.
“This will allow them to be more diversified, have a longer fishing season and be more profitable. Fishermen it seems, always find a way to adapt to the changes in the industry and persevere. We will be there with them side-by-side to help make this happen.”
The optimism expressed by industry leaders, such as Rick Young, seems to be contagious throughout the Eastern Canadian fishery.
After years of uncertainty, combined with the constant nattering of the naysayers mumbling about how the fishery will soon be no more, the industry is on the upswing – driven by positive factors that could help this still valuable business turn the corner and further increase in value.
Just as sure as the strong Northeast winds will continue to buffet the shores each year, those prosecuting the seafood industry in Eastern Canada will stand by their resolve and continue to produce the products that continue to drive the growth and evolution of this critically important, multi-billion dollar machine called the fishery.
ABOUT THE AUTHOR
Kerry Hann is the Managing Editor of The Navigator Magazine, the largest publication covering the marine and fishing industries in Eastern Canada. Hann, based in St. John’s, Newfoundland and Labrador, has been covering the North Atlantic fishery and other natural resources-based issues in various capacities for nearly 25 years.
AUGUST 1, 2016 — Wilson Sons Ultratug Offshore, a joint venture between Wilson Sons and Chilean maritime services provider Ultramar, has taken delivery of a Damen PSV 5000, built at Wilson Sons
Marine Log: Tell us about the history of The Pasha Group
George Pasha IV: The Pasha Group is a family-owned, third-generation diversified global logistics and transportation company. My grandfather, George W. Pasha, II, known to many as “Senior,” founded the company in his second career. He was an automotive engineer and worked for distributors of the early classic cars such as Duisenberg, Cord and Velie, selling and servicing their products. He purchased a “Flying A” service station across the street from Fort Mason in San Francisco in December 1941, five days after the attack on Pearl Harbor. The station was an immediate success mainly due to my grandfather’s reputation as an excellent mechanic.
A year later, Senior expanded his operations to provide storage for privately owned vehicles of World War II personnel assigned overseas. This eventually led to the 1947 incorporation of the first Pasha business, Pasha Overseas Automobile Processing Company.
Over the next 20 years, the company grew, especially when George W. Pasha, III (my dad) joined his father and established the first independent automotive port processing terminal on the West Coast at Fort Mason and a body shop on Fisherman’s Wharf to service, repair, and provide a “showroom ready” product. Inheriting his father’s keen business sense, “George III” expanded the company over the years by establishing state-of-the-art automobile facilities up and down the West Coast and in the mid-Atlantic. Today, we market automotive processing services at the Ports of Grays Harbor, WA; San Francisco and San Diego, CA; Baltimore, MD; and Manatee, FL. Our facility in National City Marine Terminal opened in 1990 and has processed over 5 million vehicles to date.
My dad formed a stevedoring and trucking company alongside the auto terminal business to create a comprehensive logistics solution from unloading of inbound vessels to delivery to dealers. In 1972, Pasha Maritime Services was formed and the stevedoring business diversified, adding break-bulk and general cargoes of all types to the service offering. In 1987, Pasha opened an omni-terminal at berths 174-181 in the Port of Los Angeles to provide stevedoring and terminal services of steel products including steel slab. The local company was renamed Pasha Stevedoring & Terminals, as it’s known today.
In the 80’s, the company diversified in the domestic and international logistics business and Non-Vessel Ocean Common Carrier businesses largely through acquisition. One such acquisition was AFI Worldwide Forwarders, one of the pioneering forwarders serving the household goods moving requirements for the U.S. Department of Defense. This expansion brought the company to many corners of the globe.
Both my grandfather and dad had an affinity for Hawaii. My grandfather arranged shipment of military members’ privately owned vehicles to and from Hawaii out of San Francisco. In the 90’s, the company arranged for shipment of new cars for several of our OEM clients. In 1999, the company formed Pasha Hawaii and commenced ocean service between the Mainland and Hawaii in 2005, introducing the first Jones Act-qualified, modern pure car/truck carrier to the domestic trades. The MV Jean Anne, named after my grandmother on my dad’s side, has ably served the market providing efficient carriage of autos, trucks, buses and rolling stock of all shapes and sizes including Stryker tactical wheeled vehicles, rail cars, and construction material and equipment.
In 2015, we welcomed the MV Marjorie C, a combination container/roll-on/roll-off (ConRo) vessel. The Marjorie C, named after my grandmother on my mom’s side, is the only one of its type to ply the Mainland/Hawaii trade lane. The 26,000-ton vessel was engineered from a proven design by Grimaldi in Croatia at Uljanik Shipyard and is the largest ever built at VT Halter in Pascagoula, Mississippi. Pasha Hawaii added Marjorie C to not only offer increased Ro/Ro service to existing customers, but to diversify our service offering by expanding our container capabilities and frequency of service.
Quickly following the introduction of the Marjorie C into the Mainland/Hawaii trade, The Pasha Group also expanded operations via the acquisition of Horizon Lines’ Hawaii business units, and welcomed team members from Horizon Lines and subsidiaries Hawaii-based Hawaii Stevedores, Inc. and the California-based operations of Sea-Logix, LLC. In addition to adding four U.S.-flag, Jones Act containerships, the growth in overall scale and associates supporting these Hawaii business units resulted in a nearly doubling in size of The Pasha Group.
This month, Pasha Hawaii is enhancing service for both container and Ro/Ro cargo from the West Coast to Hawaii Island, with the addition of the Marjorie C providing direct service from Los Angeles to Hilo.
This new route complements the Jean Anne’s current bi-weekly service from San Diego to Hilo. By recently deploying all four container ships to service our LA-Hawaii Express (LHX) and CA-Hawaii Express (CHX) routes, we were able to adjust Marjorie C’s route to include a fast, reliable, 5-day direct call from Los Angeles to Hilo and bring weekly roll-on/roll-off service to Hawaii Island.
ML: How did you get started in the marine business?
GP: I was always fascinated and proud of the business my grandfather founded and my dad diversified and built. I spent summers working for the company gaining experience in all of our divisions. After I received my Economics degree from the School of Business at Santa Clara University, I entered the world of finance, joining Wells Fargo Bank’s training program with the intent of pursuing a career in international banking.
The 80’s were a period of rapid growth and my dad asked me to join him and manage part of our forwarding and logistics divisions. To be able to support my dad in his endeavors was very rewarding. As the oldest of five children, I’ve always felt a great responsibility to both my family and the company. Together my dad and I successfully expanded the scale and breadth of the company. In 2008, I was appointed CEO and assumed responsibility for all divisions of the company, still working very closely with our Chairman, George III.
ML: Tell us about The Pasha Group shipping and logistics business model. How has it evolved over the years since your business first started in 1947?
GP: Growth has been strategic and measured with the goal of having the infrastructure, resources, and capabilities to become a world leader in diversified global logistics and transportation services. Growth and diversification has been largely organic, endeavoring to realize synergies between the divisions and staying close to what we understand and do well. Great effort has been made to stay true to our family values, and through them we strive to support a highly performing group of professionals whose mission is to deliver excellence to a broad base of world-class clients.
The model for many years was asset light. People and property leases in strategic locations were our most important assets. In an effort to allow the company to remain relevant and competitive for another generation or more, beginning with the construction of the MV Jean Anne, we have become a very capital intense business. In 2015, we invested more than $350 Million in our business – a large departure from asset light. However, our newest vessel, the Hawaii assets of Horizon Lines and other transportation assets are all very complementary to the core business. We have leveraged off of the existing organization and internal competencies while complementing with the experienced management, operators and sales folks that joined us from Horizon.
ML: Last year, Pasha added the Marjorie C. Have you been pleased with the performance of the new vessel? Do you have plans to add additional RO/RO vehicle carriers?
GP: Marjorie C has proven to be a great fit for the Hawaii trade. The ConRo vessel has improved our service capabilities through increased capacity and frequency for autos and oversize cargoes as planned. With her unique design, she offers great flexibility by serving a dual role of providing container service while simultaneously serving our Ro/Ro customers. We have also been able to directly call the neighbor islands. Marjorie C features the latest in fuel and emission savings including a shaft generator which uses excess power from the main engine to support electrical needs together with powering of reefer containers.
We are currently actively engaged with the U.S. shipyards to develop our vessel investment strategy. The strategy will balance the needs of the trade, Pasha’s strengths and the opportunity to embrace the latest technologies to assure efficient carriage of goods between Hawaii and the mainland.
ML: Last year, Pasha acquired the Hawaii operations of Horizon Lines. What assets and personnel did that involve and how has the integration of those assets been progressing?
GP: Pasha acquired nearly 900 California and Hawaii-based team members that supported Horizon’s Hawaii business, as well as its subsidiaries Hawaii Stevedores, Inc. (HSI) and Sea-Logix, LLC. In addition, we formed a Dallas service center and brought more than 30 ex-Horizon professionals aboard in that office.
Pasha now owns four former Horizon U.S.-flag container ships (Spirit, Reliance, Pacific and Enterprise) operating alongside Jean Anne and Marjorie C. This provides our customers with increased cargo capacity and the widest range of ocean transportation services between Hawaii and the Mainland. We also expanded our ports to include Los Angeles and Oakland, and more than doubled the frequency of our sailings.
HSI provides us with our own experienced manpower to load and offload cargo in Hawaii, and with Sea-Logix, we now have our own container trucking fleet to pick up and deliver our customers’ cargo, as well as provide trucking to other companies. Adding these businesses has strengthened our integrated shipping and logistics offering to our customers and leveraged synergies within The Pasha Group as a whole.
It’s been a year since the acquisition and the integration of our new employees and assets. The transition has progressed very well. Our success with this very large and complex transaction is due to the dedication of our employees, both current and former Horizon personnel, all of whom share Pasha’s key core values of teamwork, innovation and excellence.
Combining the two businesses allowed us to more effectively serve our expanding customer base while maintaining our customer service philosophy.
ML: Operators are under tremendous environmental regulatory pressure. How has Pasha addressed the issues of emissions, ballast water treatment and sustainability in its operations?
GP: Environmental management is one of the key responsibilities of our in-house Performance Management Team. Route planning, heat balance, hull resistance, and engine performance are just a few of the parameters regularly analyzed to ensure optimum performance on all of our vessels. We currently have projects underway to install stack analyzers and automatic engine tuning to further increase our fuel efficiency and reduce emissions. Through our Ship Energy Efficiency Management Plan we provide the most up-to-date guidelines to our crews for energy conservation.
We are in discussions with Ballast Water Treatment manufacturers and have completed engineering reviews. Currently there is not a USCG approved unit available. When approved systems become available we are prepared. Currently we minimize all ballast water exchange.
Environmental sustainability is important to Pasha and we support long-term ecological balance. We are studying alternative fuels with less environmental impact such as liquefied natural gas. The use of reusable or recycled products is encouraged.
To help eliminate pollution from port-related operations, we are also very proud to announce recently that our Pasha Stevedoring & Terminals L.P. team at the Port of Los Angeles is partnering with the Port to launch the Green Omni Terminal Demonstration Project, a full-scale, real-time demonstration of zero and near-zero emission technologies at a working marine terminal. At full build out, Pasha will be the world’s first marine terminal able to generate all of its energy needs from renewable sources.
ML: What do you see for the future of Pasha? What lessons could you impart to other operators regarding best practices?
GP: The next several years will entail filling in our organization to bring our standard as close to excellence as we can. Meanwhile we will focus on fundamentals of continuing to invest across the company in a balanced way that will promote health and growth across all of our divisions.
The birth of VesselsValue was driven by timing and need. In 2008, the crisis in the financial market extended into shipping. The dry bulk sector and the containership sector were hit the hardest, and while tankers remained relatively buoyant, banks needed to assess their capital commitments against the value of the assets being financed and being used as collateral. However, in the depth of the crisis (2010 / 2011), ship brokers were telling clients they could not value the ships as there had been no recent sale or “last done” in ship broker speak. Richard Rivlin, a sale and purchase broker with 30 years’ experience, had long felt that an automatic valuation system could be built, which would produce valuations in any market, at any time. Luckily, his brother is a Professor of Mathematics, and together they designed and built such a system. It quickly became apparent that the highly detailed multi-level regression model was far too complex for normal spreadsheets, and a specialist modelling company was employed to develop the model.
The model is fed by two databases. One contains the features and specification of the ships arranged in a unique structure that allows the computational model high speed access. This database is researched and compiled by VesselsValue own team of 30 researchers and analysts on the Isle of Wight in the UK. The second database consists of sale and purchase transactions and charters. Both feed the mathematic model which is operated by a team of quantitative analysts. The aim was to produce an instant, accurate and always available online ship valuations for the banks and finance houses, that form the main customers of VesselsValue.
Tankers Valuation
According to VesselsValue, five factors make up a valuation:
Each factor is broken down into further elements that are scored. As an asset, tankers are relatively straightforward, being highly commoditized, and standardized in terms of size ranges and specification. In part this is due to the international safety and pollution control legislation that has been forced on the tanker sector. This level of standardization makes VesselsValue task somewhat easier when it comes to scoring the factors, than offshore vessels, which have just been added to the system. In the case of tankers, there are around 140 scores. One of the most important scores is the shipyard. A vessel built in China is less desirable than one built in Japan. A well-published example is the one shown above. In November 2014, the New Century-built Supramax bulker ACS Diamond was sold for $10 million. The previous week, the slightly older Japanese-built pair of Supramaxes were sold for $15.5 million each. This was an implied discount of around 40% between Japan and China. However, the shipyard scoring goes into several levels of sophistication, including many ships the shipyard has built and when the last vessel was constructed.
This model is continually updated and recalibrated overnight to give the closest possible fit to the reported sales prices. It is the analysis of the sales that can produce the weightings required for different shipyards. These are applied to all shipyards, not just Chinese shipyards.
So far VesselsValue have performed over 1,000,000 valuations to date, about 400,000 a year and the number is increasing.
How Accurate is VesselsValue?
The split of VV customers are banks and finance houses, owners and other maritime industries such as lawyers, insurers and charterers – sophisticated market participants who insist on knowing the methodology behind our valuations. But ultimately they want to know how accurate are our valuations because this will affect their bottom line. Valuation accuracy is assessed as the difference between the price a vessel is sold at, and VV valuation on the day before the actual sales date. This is expressed as a % of valuations within a certain band of accuracy and shown in a chart form. The accuracy report is available on the website.
Tanker Valuations Development
According to the VesselsValue transactions database, between the start of 2012 and May 2016, a total value of $143 billion of tankers have been traded on the sale and purchase market. During that period the value of second-hand tankers has steadily increased, as can be seen from figure 1 (“VV Tanker Matrix”) below of the VV Tanker Matrix, expressed as USD / DWT.
During that period, the MR tanker has been the most frequently traded tanker type, both in terms of number of sales, and value (see figure 2 “Total Value by Type of Tankers Sold 2012 to Date”).
So far in 2016 (to 15 May 2016) 83 tankers with a total value of $1.4 billion, have been traded on the second-hand market, and again the MR tanker is the most popular (see figure 3 “Value of Tankers Sales Jan 2016 to YTD).
Interestingly, the average age of MR2 (Chemical / Product) tankers sold in the first five and half months of 2016 is only three years-old. Altogether 17 of these vessels were sold in this period, with eight tankers being sold by owners in the USA (these were not Jones Act vessels).
The majority of tankers and the largest value of tankers sold so far this year (2016) were constructed in South Korea, followed by Japan and China. As far as owners are concerned, the lead seller across all types of tankers was Chembulk Tankers, Scorpio Tankers and companies associated with the Navig8 group (see figure 4 “Top Ten Sellers of Tankers Ranked by Number of Vessels Sold”).
Recent Sales of Interest
The top three sellers have sold tankers for completely different reasons and strategy. In January 2016, Chembulk Tankers was sold by parent company Berlian Laju Tanker (BLT) to private equity investor Kohlberg Kravis Roberts (KKR). Chembulk Tankers is said to have a number of Contracts of Affreightments (CoAs) and the older tankers were surplus to requirement. This is part of the KKR growth strategy to rebuild the Chembulk Tankers fleet. KKR has also invested in a fund to invest in two Greek bank shipping portfolios.
The number two top seller, Scorpio Tankers, was a tactical, opportunistic sale. The purchaser, Bahri (formerly known as National Chemical Carriers of Saudi Arabia) is on something of a buying spree. Bahri has recently purchased two VLCCs from Tanker Investments in December 2015, for a reported $77.5 million. The five 2014-built MR2 tankers were sold en bloc for $167 million are trading in the UAE under Bahri CoAs.
The third most active seller, Navig8 Chemical Tankers, Inc., sold the four resales (the MR2 tankers are due for delivery in 2017) under a ten-year bareboat charter (with purchase option) for a reported $35 million each. This was an internal sale within the group, and part of a longer term strategy.
Last year, the agency announced that it would order a new series of vessels—up to 37 in total for about $450 million— known as the Maneuver Support Vessel (Light), MSV(L) for its watercraft fleet. At print time, no RFP had been released, but it is expected to be issued in the next few weeks. The Army currently has a fleet of 132 vessels that perform a large percentage of the U.S. forces’ equipment and supply deliveries. Missions for the fleet are broken up into four categories: (1) Landing Craft; (2) Ship-to-Shore Enablers; (3) Towing and Terminal Support Operations; (4) Watercraft Operations Support.
The U.S. Army’s fleet is meant to be deployed worldwide, and can support operational movement and maneuver and force repositioning. Additionally, the agency says, the vessels perform a variety of roles.
Vessel type is broken up into two categories:
Details on the MSV(L)
The upcoming MSV(L) will replace the Landing Craft Mechanized 8 (LCM-8) (pictured above), which has been in service since 1967. The LCM-8 travels at 12 knots with no load and 8 knots or less with load. The LCM-8 is small in size, measuring just 74 ft x 21 ft, and can be used in confined areas. It has a range of 332 nautical miles unloaded and 271 nautical miles loaded. Designed for operations in rough waters, the LCM-8 can maneuver through sea state 3, breakers and can ground on a beach. Its bow ramp enables roll-on / roll-off (RO/RO) operations with wheeled and tracked vehicles.
The MSV(L) will feature an increased payload and speed over its predecessor, LCM-8.
The introduction of the MSV(L) into the fleet, says the Army, “will enable the agency to meet its movement, maneuver, and integrated expeditionary sustainment requirements with a more agile, versatile; and capable platform. The MSV(L) will conduct movement and maneuver of tactical force elements as well as traditional Army Watercraft System sustainment operations.”
The MSV(L) will also be able to operate in a variety bodies of waters including coastal waters, rivers and narrow waterways.
According to the agency, Col. Michael M. Russell Sr. Army G-8 FD Division Chief, called the MSV(L) program a lynchpin to the Army’s watercraft strategy. The landing craft will have the ability and capacity to carry a tank, a Joint Light Tactical Vehicle (JLTV), a Stryker armored fighting vehicle, troops, or supplies.
Russell added that the system would not be designed from scratch, and will likely be based on an existing design that will be “ruggedized” and made to fit the Army’s mission profile.
Industry Players Express Interest
One of the designs expected to be in the running is Constructions Industrielles de la Méditerranée’s (CNIM) L-Cat design.
Last December it was announced the CNIM would team up with Fincantieri Marine Group (FMG), the U.S. subsidiary of Fincantieri, Oshkosh Defense, LLC, and Watercraft Logistics Services (WLS) to pursue the contract.
The L-Cat (Landing Catamaran Craft) is an innovative and rapid amphibious ship with a RO/RO design that integrates a mobile loading platform in a catamaran hull. This enables for personnel, armored vehicles and equipment to be unloaded in areas where there are no port facilities and shallow waters.
Intended for shore-to-shore applications, the L-Cat is already successfully used by the French National Navy, under the name EDA-R.
CNIM says that “during amphibious operations, it (the L-Cat) guarantees optimal transit speed, rapid loading and unloading of the deck.” This helps reduce threat during exposure time and offers a high degree of autonomy, with the vessel able to operate in a rage of 500 to 700 nautical miles, depending on the load.
Measuring 30 m x 12.6 m, the L-Cat has a maximum payload capacity of 100 tonnes, can reach speeds of up to 30 knots when empty and 18 knots when loaded to maximum payload.
The design’s proven track record, along with its own successful history of building vessels for the Army, Coast Guard and Navy, makes the group the optimal choice for the MSV(L) build program, according to Francesco G. Valente, President and CEO of FMG. “We believe that our world-class team and proven design represent the lowest risk and lowest total life-cycle cost to the U.S. Army,” said Valente.
Valente notes that FMG shipyards—Fincantieri Marinette Marine, Fincantieri Bay Shipbuilding and Fincantieri Ace Marine—have experience in building these types of landing craft, having built the LCM-6, LCM-8 and LCU landing craft in Marinette. The shipbuilder has also had the distinction of building 562 landing craft for the Army and Navy over a period of 23-years. And Marinette Marine was also half of the RB-M team (Kvichak Industries the other half) that built the Response Boat-Medium for the U.S. Coast Guard.
Meeting Production Needs, Who Wants In?
According to the Army’s MSV(L) DRAFT-Production Schedule, it is expected that one prototype will be built and tested by FY19, four will be built during Low Rate Initial Production (LRIP) between FY 21 and FY 22; and, should the program reach full scale production, 32 will be produced during a four-year period between FY23 through FY27.
Kvichak, formerly known as Kvichak Marine Industries, now part of the Vigor group of companies, could also be a contender should it choose to pursue the contract.
The boat builder is listed on the Army’s list of Interested Prime Contractors along with Bollinger Shipyards, Conrad Shipyards, Ingalls Shipbuilding, Derecktor, Sterling Shipyard, Swiftships, LLC, and United States Marine, Inc.—the list is a prime example of the variety of yards interested in the contract, as well as the agency’s willingness to open up the contract pursuit to all shipyard types.
Kvichak is no stranger to producing vessels for government agencies in a full-scale production cycle, having long been a builder of pilot and patrol boats. Most notably, Kvichak was the other half of Team RB-M. The team built and delivered 174 RB-Ms for the Coast Guard, on time and on budget, completing the program in 2015.
The other builders on the list also have diverse portfolios, making each a feasible choice for the MSV(L) program.
Bollinger has long been a builder of patrol vessels for both the U.S. Coast Guard and U.S. Navy. Most recently delivering the 17th Fast Response Cutter to the U.S. Coast Guard.
Conrad has, perhaps, the most diverse portfolio, with experience in the construction, conversion and repair of a wide variety of steel and aluminum marine vessels across its shipyards for both commercial and government customers—Conrad’s Orange shipyard has produced a number of vessels for the army. Conrad, as most are aware, is currently building the first LNG bunker barge for operation in U.S.
Derecktor could put itself back in the shipbuilding game big time, should it win this contract. The yard has seen its share of trouble over the last decade, having filed for bankruptcy in Connecticut and losing its Bridgeport facility in the process, but Derecktor is putting in the work to get itself to the level it once was. The builder has experience building a variety of innovative vessel types both in the commercial and private yacht sector, including ferries, security vessels, patrol crafts, research vessels and workboats.
Ingalls Shipbuilding, a division of Huntington Ingalls Industries, has an extensive history with both the Coast Guard and Navy. Ingalls is currently building vessel 6 through 8 in the National Security Cutter Program for the Coast Guard’s fleet at its Pascagoula, MS shipyard. Under the program, eight vessels will be built to replace the aging 378-ft high endurance cutters. The shipbuilder also recently announced that the U.S. Navy’s 10th San Antonio-class amphibious transport dock, John P. Murtha (LPD 26), successfully completed acceptance trials. Under its contract with the Navy, Ingalls has built and delivered nine ships in the San Antonio Class. LPD 26 will be delivered in May. The 11th LPD, Portland (LPD 27) will be christened later this month. The yard has also received advanced procurement funding for long-lead-time material for the 12th ship in the series, the LPD 28.
Texas-based Sterling Shipyard, started by Harry Murdock and Brad Taylor, formerly of Orange Shipbuilding, has built a number of tank barges and towboats.
Swiftships specializes in the construction of small to medium-sized vessels made with steel, aluminum and fiberglass. It has delivered boats to the U.S. military, both commercial and private companies and 52 foreign countries.
United States Marine, Inc., Gulfport, MS, a designer and builder of fast patrol and special operations craft for the U.S. and foreign militaries, has predominately been a builder of military, patrol and special warfare boats in the 21 ft to 90 ft range. In its 30 plus years in business it has delivered over 500 craft to the U.S. Navy, USSCOCOM, NAVSEA and foreign militaries.
Oil and gas E&P generates billions of dollars worth of business annually for shipyards in the form of newbuilds, conversions, and ongoing repairs and maintenance. With the downturn in oil, however, much of that business has dried up and forced shipyards that depend on the oil patch to rethink their strategy. Many are repositioning themselves to pursue other markets or are undertaking capital investments in their facilities to be more efficient and competitive.
There’s no better example than VARD Holdings, one of the world’s largest shipbuilding groups, whose portfolio is heavily focused on offshore oil and gas. Amid losses of NOK1.29 billion (about $148 million) VARD said last month it would preserve its core expertise and skilled employee base and use its existing shipyard capacity until an eventual recovery in its core market. Among the areas it was pursuing were the offshore wind and aquaculture markets. It will also work more closely with its major shareholder, Fincantieri, to support the cruise vessel and offshore patrol vessel sectors.
NORTH AMERICAN SHIPYARDS INVEST, DIVERSIFY
While operators in the Gulf of Mexico have cold stacked many of their vessels, Galliano, LA-based Edison Chouest Offshore, one of the world’s largest offshore support vessels operators, announced last month that it would invest $68 million in opening a new shipyard in the Port of Gulfport, MS. The shipyard, called TopShip, LLC, will operate at the former Huntington Ingalls Composite Facility, which was acquired by the Port of Gulf Port last March.
The new yard was made possible through an incentive package from the Mississippi Development Authority that would help bring TopShip to the port and create over 1,000 jobs, according to Jonathan Daniels, Executive Director and CEO of the Mississippi State Port Authority—the job creation would prove a significant boost to the local economy.
Lawmakers approved an $11 million package through the Mississippi Major Economic Impact Authority—with $10 million going to discretionary funds and $1 million allocated for workforce training. Additionally, the Port has said it would provide $25 million in Katrina-CDBG funds for infrastructure improvements.
ECO already operates shipyards in the U.S. and one in Brazil: North American Shipbuilding, Larose, LA, LaShip, Houma, LA, Tampa Ship, Tampa FL, Navship in Brazil, and Gulf Ship which is also in Gulfport. Most of ECO’s fleet has been constructed at one of its yards.
Having been born in Mississippi, Gary Chouest, ECO President and CEO expressed his gratitude towards the state for the opportunity to provide quality service to its customers, and help the community thrive.
“We are indeed excited about the opportunities to grow TopShip in a business friendly state, one where we can reach out into the community to recruit various skill sets, developing a quality workforce that will allow TopShip not only to compete locally, but also globally,” said Chouest. “With the help of the state of Mississippi, we will modify our TopShip facility to become one of the safest and most efficient shipyards in the nation, building Chouest pride for our employees.”
Mississippi’s VT Halter Marine, too, has seen how investing in its facilities can help business. Over the last 10 years, VT Halter has invested over $100 million to upgrade its three facilities in Mississippi. This includes expanding beyond the newbuild business with a $13 million investment in a new drydock and repair facility back in 2015, the addition of a blast and paint facility; and the purchase of a 76,000 ft2 climate-controlled warehouse.
The investments have not only allowed growth into the repair business, but also made VT Halter Marine more efficient in its newbuild projects, enabling it to meet the growing demands of the increasingly popular Articulated Tug and Barge (ATB) market. Most recently, VT Halter completed the second of two 250,000 bbl ATB units for Bouchard Transportation (see this month’s CEO Spotlight); and currently is preparing the delivery of the second of two 130 ft, 6,000 hp ABS class ocean towing ATB tugs for Bouchard.
VT Halter Marine is also currently building two 2,400 TEU LNG-powered combination ConRo ships for Crowley Maritime Corporation’s liner services group. El Coquí and Taíno will operate in the Jones Act trade between Florida and Puerto Rico and will offer a 38% reduction in CO2 emissions per container. The ships will be delivered by VT Halter Marine in 2017.
Another yard that has benefited from the use of Liquefied Natural Gas (LNG) as a marine fuel is Conrad Industries. The last few years has seen Conrad Industries, Inc., Morgan City, LA shifting its business approach and diversifying its portfolio—among the shipbuilder’s offerings, it builds tugs, ferries, ocean tank barges, liftboats and specialty barges. In 2015 the yard’s orderbook received a much-needed boost with new construction contracts, including the history-making construction of the first LNG bunker barge for the North American market.
Currently under construction at Conrad’s Orange Shipyard, Orange, TX, the 2,200 m3 capacity bunker barge is being built for WesPac Midstream LLC. Designed by Bristol Harbor Group, Inc., Bristol, RI, and built to ABS class, the barge when delivered later this year will serve TOTE’s Marlin class containerships—Isla Bella and Perla del Caribe, both built at General Dynamics NASSCO. Those LNG-fueled ships are already operating in the Jacksonville to Puerto Rico trade.
It was also certified by GTT to construct the special LNG containment system on the LNG transport bunker barge.
The shipbuilder has also broadened its offerings further with the expansion of its Deepwater South facility in Amelia, LA. The 52-acre site has enabled Conrad to build large articulated barge units. Currently there are eight tank barges under construction at Deepwater South—ranging from 55,000 bbl to 83,000 bbl capacity.
Conrad says that Deepwater South will undergo a wide range of improvements this year including the addition of a new fabrication and assembly building—which will allow for the uninterrupted construction of hull modules year round; and a new Panel Line Building—expected to begin operations this April. The Panel Line Building will be equipped with an automated welding system, a stiffener fitting gantry to automate the fit-up of stiffeners on the panels, and an 8-headed automated stiffener welder—allowing for the shipyard to process 350 tons of steel per week.
THREE NEW FAB BAYS
C&C Marine and Repair, Belle Chasse, LA, is focusing on increasing efficiencies to maintain its competitive advantage. The yard recently added three new fabrication bays giving C & C an additional 115,000 ft2 for the construction of boats and barges; and a fabrication area of 230,000 ft2.
Over the next few months, the yard plans to order two additional transporters (it currently has two capable of moving 600 tons) with a capacity of 830 tons, bringing the total capacity of its transporters to 1,430 tons. This, says New Construction Manager Matthew J. Dobson, will create new opportunities for the yard, and enable C & C to begin taking orders for the fabrication of new 30,000-barrel barges and allow it to transport larger vessels to land for repair projects and paint jobs.
The yard currently has 29 new construction vessels under contract including three 6,600 hp towboats, one 280 ft PSV, one 270 ft cutter head barge, sixteen tank barges and eight deck barges of various sizes.
EXPANDING INTO LARGER VESSELS
Back in 2014, Metal Shark Boats, Jeanerette, LA, was already a successful builder of aluminum vessels, but it had its sights on the construction of vessels up to 90 ft in length and larger, as well as expansion of its portfolio to include steel. It also signed a technology agreement with Damen that would allow it to build offshore patrol boats up to 165 ft in length.
With the development of the new shipyard in Franklin, LA, Metal Shark, now employs 230 workers between its boat yards, and is among the busiest boatbuilders in the U.S., currently producing a number of 38 ft, 45 ft and 55 ft Defiant class vessels and constructing large orders for the U.S. Coast Guard, U.S. Navy and multiple agencies across the U.S. It also delivered a sophisticated 75 ft multiple purpose port security fire boat to the Port of South Louisiana.
EYE ON THE CARIBBEAN MARKET
For St. Johns Ship Building, diversification of its portfolio and the markets it reaches will propel its next evolution. The small shipyard, which has been under private ownership since 2006, recently delivered the first Elizabeth Anne class of towing vessels to the Vane Brothers Company. The tug is the first in a series of eight the Palatka, FL-based yard is building for the operator. At press time the second vessel was in the water and the third was about to be launched.
St. Johns Ship Building’s yard sits along the St. Johns River—giving it the unique advantage of being on the East Coast with access to both the Gulf of Mexico and the Caribbean—and its because of its location St. Johns has been able to produce such a diverse portfolio. From OSVs to tugs (a new market for the builder), to coast guard vessels and cargo ships, St. Johns’ 100 acre facility and its 150 employees are at the ready to take on any project.
St. Johns Ship Building President Steven Ganoe says that because the yard doesn’t solely rely on the oil and gas market it has been able to keep business steady during the downturn in the oil and gas market.
Ganoe says the shipyard is keeping tabs on the Caribbean market to see how it develops in the wake of the easing of restrictions on Cuba travel—and determine how St. Johns can help meet any growing demand in that specific market. In the meantime, the shipbuilder continues to make improvements to its facility—having recently added an 18,000 ft2 assembly shop and a Messer CNC 80 ft table to help make production more efficient.
REBORN AS WORLD MARINE
Earlier this year it was announced that World Marine LLC—owned by the Teachers’ Retirement System of Alabama and the Employees’ Retirement System of Alabama—had bought all of Signal International’s assets including its full service and heavy fabrication facilities in Mobile, AL and Pascagoula, MS.
According to the Chapter 11 plan of liquidation, World Marine is seeking to become a leader in the ship repair and ship construction market.
World Marine assures that its experienced team—led by Dick Marler—can handle all types of vessels, but the company will place a high focus on new construction, and the repair and conversion of ocean going vessels and offshore drilling rigs—serving the energy, government and commercial marine markets.
World Marine’s construction and repair facilities include three drydocks—a 22,000-ton Panamax class, a 4,200-ton, and a 20,000 MT heavy lift. The company says its future plans include pursuing the emerging LNG market for the construction of bunker barges and transfer vessels.
NEW DRYDOCK AT COLONNA’S
A decade after the American Civil War ended, Colonna’s Shipyard was founded by Charles J. Colonna. Now, 140 years later, the yard continues to operate and develop with the times.
The shipyard currently occupies over 100 acres of land in the Berkley section of Norfolk, VA, and has water access to over 3,000 ft of vessel berthing space and a lift capacity to accommodate vessels up to 850 long.
Colonna’s is also home to the largest Travel lift in the U.S.—with a capacity of 1,000 metric tons.
As part of its future improvement plans, Colonna’s expects to purchase an additional 25 acres across the street from its main entrance, and add a new floating dry dock.
A few months ago, the Governor of Virginia, Terry McAuliffe, announced that the yard would undergo a significant expansion, with Colonna’s investing over $30 million to expand its operations in the City of Norfolk. The expansion would include a new larger drydock, dredging and improvement work to the channel and bulkhead work, and the creation of 51 jobs to the area.
The new floating drydock, which will be named the Charles J., will have a lifting capacity of 11,500 metric tons, an overall length of 595 ft and an inside width of 108 ft. The Charles J. is expected to be fully operational in early 2017 and will accommodate a variety of vessel types including ferries, tugs, barges, containerships, OSVs and several type of government vessels.
Colonna’s CEO Tom Godfrey, said the capital investments would “allow Colonna’s to continue to provide quality services to both commercial and government customers throughout the region.”
NEW DRYDOCKS, AT BAE, DETYENS, BAY SHIPBUILDING
Meanwhile, South Carolina-based Detyens Shipyards recently took delivery of its new floating drydock. Built by Corn Island Shipyard, Grandview, IN, the 400 ft x 108 ft drydock will enable the yard to provide a more cost-effective service to smaller tonnage vessels.
According to Detyens, in the past, smaller vessels would have to piggy back in the yard’s larger graving dock—now with the addition of the smaller dock, it can provide drydock services to vessels up to 11,000 DWT. The new dock sits along the yard’s F Pier, which recently underwent upgrades that included the addition of shipyard services, additional lighting, and dredging of 30 ft.
On the U.S. West Coast, BAE Systems is investing $100 million to build and install a second, larger drydock at its San Diego shipyard. Currently under construction in China, the 950 ft drydock will have a lifting capacity of 55,000 long tons and is expected to support the expansion of the Navy ships homeported in San Diego, which are expected to increase by 20 from 60 to 80 by 2020, according to BAE’s Director of Communications, Karl Johnson. BAE Systems is among the leading providers of maintenance and modernization services of the U.S. Navy.
Portland, OR, Vigor Industrial has been aggressively growing its business through the acquisition and merger with several other regional shipyards, including Kvichak Marine Industries, Seattle, WA.
In 2014, Vigor’s Portland yard began operating its new $50 million drydock, the Vigorous. It has been consistently booked since, supporting hundreds of jobs and attracting work that could not have previously be performed in the region, according to Vigor’s Athena Maris.
Vigorous, with a lifting capacity of 80,000 long tons, is 960 ft long with an inside width of 186 ft and has taken on several repair work projects including the repair work on cruise vessels, and most recently, this past summer, on repair the hull of the multipurpose icebreaker on charter for Shell, the MSV Fennica.
The addition of Vigorous at the Portland yard, enabled Vigor to also reinvest in some of its existing assets. Specifically, Vigor was able to upgrade and transfer one of Portland’s drydocks to its Seattle facility. In Seattle, the drydock Vigilant will be used to perform repair work on the recently awarded Structural Enhancement Drydock Availability (SEDA) Projects. There, the U.S. Coast Guard cutters Bertholf and Waesche will both undergo significant structural enhancement work, system upgrades and maintenance.
Beyond that Vigor is placing capital investments efforts on its environmental stewardship—this includes working on a comprehensive storm water management system at its Portland facility and a shallow-water estuary to help increase the survival of young salmon and steelhead trout on their way to the ocean at its Seattle facility.
On the Great Lakes, Fincantieri Bay Shipbuilding (FBS) parent, Fincantieri Marine Group (FMG), has invested more than $33 million in capital improvements to increase manufacturing capabilities at its facility in Sturgeon Bay, WI. FMG is currently in negotiations to acquire additional property adjacent to the shipyard to further expand its serial production capabilities.
FBS has completed its new Pipe/Outfitting Building & New Welding Center and added a new floating dry dock that has a total lift capacity of 7,000 long tons. The versatile dry dock can be sectioned off, with a 216 ft section and a 432 ft section.
It has completed the expansion of its Fabrication Building and has added a new Beveling Plasma Burning Machine, 200-ton Yard Transporter, IMG Micro Panel Line, and 1000-ton CNC Press.
Back in 2012, FBS added a 45 ft x 47 ft “megadoor” to the south end of its Fabrication Building 311 to allow larger vessels to be built indoors and moved outside for launching and a Manitowoc 300-ton capacity Model 2250 Crawler Crane.
FBS employs 600 to 800 full-time shipyard professionals and expands its workforce to 1,100 to 1,200 using temporary and contract workers during the Winter Fleet repair season.
FBS currently has under construction six tugs and seven barges of ATB design. Accompanying photo shows the ATB tug Barbara Carol Ann Moran and the ocean tank barge Louisiana at the shipyard. As we reported back on February 22, the shipyard has 14 vessels undergoing a wide range of repairs and repowerings for the Great Lakes Winter Fleet.
SAN DIEGO BOATBUILDER GETS BIGGER, GREENER
Vigor, however, isn’t the only shipbuilder looking to help the environment. San Diego based Marine Group Boat Works will soon break ground on a $1.5 million green initiative that will see the yard install a solar panel system compliant with the state of California’s Solar Initiatives.
The addition of solar power comes during one of the company’s most exciting periods, says Marine Group Boat Works’ (MGBW) Leah Yam. MGBW, which has two yards in San Diego and one in San Jose del Cabo, Mexico, recently completed a $2.5 million renovation to its deepwater floating docks system, and will install the final set of docks this spring—making it fully ready for in-water repairs on vessels up to 420 ft in length.
Among MGBW’s most recent repair and retrofit projects is the $19 million refurbishment of the Golden Gate ferry M.S. San Francisco and the conversion of two high-speed aluminum Sub Chapter K San Francisco ferries for the Water Emergency Transportations Authority.
Beyond its repair business, MGBW is also making a dent in the new construction market. Since launching its new construction division in 2008, the shipyard has increased its employee numbers by about 195%, employing 185 workers. Currently, MGBW has five 60 ft aluminum dive boats under construction for the U.S. Navy—the contract calls for the construction of 16; and most recently delivered the first in a series of steel workboats to Japan—two additional boats are on their way, and twelve are on the production schedule, says Yam.
CANADIAN YARDS INVEST FOR NSPS
The end of 2014 saw the completion of Seaspan’s Shipyard Modernization project. Funded entirely by the shipyard, the $155 million project helped transform Seaspan’s Vancouver Shipyards into one of the most modern yards in Canada.
The two-year project included the addition of four new fabrication buildings—housing a sub assembly shop; panel shop with panel line; block assembly shop; pre-outfitting shop; paint and blast shop; and Canada’s largest (300 tonne) permanent gantry crane.
The expansion was integral to meeting the newbuild project requirements for the Canadian Coast Guard and the Royal Canadian Navy.
Vancouver Shipyards is currently building the first Offshore Fisheries Science Vessel (OFSV) under the National Shipbuilding Procurement Strategy (NSPS) for the Canadian Coast Guard. The 208 ft x 52.5 ft OFSV will help support scientific and ecosystem research critical to the economic viability and health of the region’s marine environment. At press time, 30 of the 37 blocks of the OFSV were under construction.
Seaspan also invested an additional $15 million at its Victoria Shipyards, upgrading its facilities with the addition of a new operation center that, according to Seaspan, would help support testing, trails and commissioning new federal vessels.
At press time, there were nine vessels undergoing refits and drydock work at one of Seaspan’s yards—including the 94 ft Canadian Coast Guard vessel Siyay with is undergoing a nine-month midlife modernization refit.
Keeping the future in mind, Seaspan is also investing in its workforce. Seaspan employs 1,500 employees across its three shipyards—Vancouver Shipyards, Vancouver Drydock, and Victoria Shipyards.
In 2015, the shipbuilder received a Canada Jobs Grant to develop e-learning tools for its expanding workforce—the goal of the funding was/is to help ensure workers have a common understanding of the shipbuilding processes, practices, and protocols.
Seaspan also recently announced that it plans to invest $2 million over the next seven years to help support teaching and research in the University of British Columbia’s naval architecture and marine engineering programs.
At Irving Shipbuilding, Halifax, NS, Canada, the company’s $330 million capital investment plan is already paying dividends. Last September, it marked the start of production of the HMCS Harry DeWolf, the first Arctic Offshore Patrol ship (AOPS) for Canada.
The ship is the first of up to 21 vessels that will renew Canada’s combatant fleet over the next 30 years under the NSPS. Irving Shipbuilding has built more than 80% of Canada’s current combatant ships.
Current direct employment at Marine Fabricators in Dartmouth and the Halifax Shipyard is about 900. Over the next two years, the workforce at both sites is expected to rise to 1,600, with over 1000 directly employed on AOPS production. In addition, total employment at Irving Shipbuilding (all operations) is forecasted to rise to over 2,500 direct employees at peak production of the larger Canadian Surface Combatant vessels that will replace Canada’s current fleet of Halifax Class frigates.
To date, the modernization at Irving Shipbuilding and the AOPS contract have resulted in over $1 billion in spending commitments.
Meanwhile, one of the oldest shipyards in North America, Chantier Davie Canada Inc., Levis, Quebec, has taken its first steps in the Resolve-Class Auxiliary Oiler Replenishment ship project. The project involves the conversion of a containership into an Auxiliary Oiler Replenishment Ship that will be delivered to the Canadian Royal Navy in 2017.
It also recently completed the refit of four of Canada’s heaviest icebreakers, as well as a bulk carrier and is a pioneer in the construction of LNG-fueled ferries.
JANUARY 20, 2016 — Inmarsat today opened a new 1,700 sq. m (19,500 sq. ft) office in Toa Payoh, Central Region Singapore.The regional hub provides a new solutions lab, demonstration capabilities, training
DECEMBER 23, 2015—While he played a major role in the founding of the U.S., Benjamin Franklin was never this big in life. As we reported last week, the day after Christmas, the