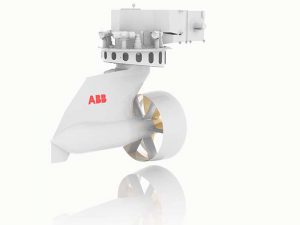
VIDEO: New Azipod XL delivers further fuel savings
SEPTEMBER 6, 2016 — ABB says that the latest version of its podded electric propulsion system, the Azipod XL, increases vessel fuel efficiency by as much as 20 percent compared to modern
SEPTEMBER 6, 2016 — ABB says that the latest version of its podded electric propulsion system, the Azipod XL, increases vessel fuel efficiency by as much as 20 percent compared to modern
SEPTEMBER 1, 2016 — Eastern Shipbuilding Group, Inc. Panama City, FL, reports that it has delivered the M/V Harvey Stone (Hull 234) to Harvey Gulf International Marine, LLC of New Orleans, LA.
Vessel operators are still very much focused on reducing fuel consumption and lowering emissions. Collaboration early on in the design of a new vessel and its construction between the vessel owner, naval architects, shipbuilders, and propulsion manufacturers can payoff in optimizing the vessel’s hull, reducing costs of construction, and lowering operational costs during a vessel’s lifetime.
“We work with naval architects early in the design process to help optimize the propulsion system, looking to meet all design requirements while minimizing the size and horsepower of the system,” says Elizabeth Boyd, PE, President, Nautican Research & Development Ltd. Boyd says collaboration early in the design phase “can result in significant savings because if the horsepower can be reduced due to efficiency gains, it can lead to size reductions in not just the horsepower and propellers, but also everything that goes along with it—shafts, bearings, etc.—sometimes it can even mean meeting the requirements with a smaller boat. We can quickly show performance and full system configuration for different sizes, allowing the naval architect to explore options very quickly.”
Nautican’s foundation was built on efficiency. More than 40 years ago, company founder Josip Gruzling pioneered the use of hydrofoils to increase the efficiency of tugs and barges. Today, Nautican engineers and manufactures hydrodynamic solutions, including patented Integrated Propulsion Units, High efficiency nozzles and propellers, high aspect ratio triple rudders, pre-swirl stators, and also hydralift skegs for barges. It says independent tests show that its propulsion system solutions increase power and maneuverability, while significantly reducing fuel use and maintenance needs.
One of the Nautican’s latest projects is fabricating the first two sets of 104-inch nozzle units for the 120 ft Kirby Offshore Marine line haul tugs under construction at Nichols Brothers Boat Builders, Whidbey Island, WA.
According to Boyd, initially nozzle development was done using both Computational Fluid Dynamics (CFD) and physical testing in a cavitation tunnel and towing tank. “However,” she says, “our CFD efforts now are focused more on integration with the hull form. For these boats, CFD was not used as the design was already well developed and fairly straight-forward as far as placing the nozzles.”
The designer of the ABS Class tugs is Jensen Maritime, Crowley Maritime Corp.’s Seattle-based naval architecture and marine engineering company.
Each of the two tugboats will be equipped with two Caterpillar 3516C main engines, rated at 2,447 hp at 1,600 rev/min. Reintjes reduction gears, supplied by Karl Senner, LLC, Kenner, LA, will turn two Nautican fixed-pitch propellers with fixed nozzles. Other equipment onboard the tugs will include two C7.1 Caterpillar generators for electrical service, one TESD-34 Markey tow winch, one CEW-60 Markey electric capstan and one Smith Berger Town Pin.
“Kirby owns many boats with Nautican systems, but most of these have been ATBs (Articulated Tug Barge units) to date,” says Boyd. “We worked recently with Nichols on a pair of Kirby 10,000 hp ATB tugs—this project went very well and these vessels are performing exceptionally well in service.”
Nautican designed larger 120 inch nozzle units for another tug for Dunlap Towing. “Dunlap is a Nautican repeat customer,” says Boyd. The new tug, says Boyd is a new design, based on the Phyllis Dunlap, but “fully rethought and redesigned by Hockema Whalen.”
The 5,000 hp, twin-screw tug Phyllis Dunlap was built in 2001 by Hansen Boat Company, Everett, WA.
“Dunlap has been a great customer to work with—they are very involved in all aspects of the design and equipment selection and are very knowledgeable, providing some really useful feedback about performance over the years in their very demanding runs to Hawaii and Alaska.”
Wärtsilä Transverse Thruster
Earlier this year, Wärtsilä expanded its transverse thruster series with the addition of the Wärtsilä WTT-40, with a 4,000 kW power level and a 3,400 mm diameter controllable pitch propeller. While Wärtsilä has designed and built customized transverse thrusters as powerful as 5,500 kW, the WTT-40 and others in the WTT range address customer needs for high power transverse thrusters for bow and stern applications.
Development work on the Wärtsilä WTT-40 began in 2015 with an eye on targeting cruise ships, large OSVs and offshore construction vessels. The high power level is particularly important for the harbor maneuvering and docking of large ships, and for dynamic positioning of offshore vessels working in heavy sea conditions.
Because of its maximum power of 4,000 kW, shipyards and cruise vessel designers have the option of using three WTT-40 thrusters instead of four smaller ones. This translates into a more efficient vessel design with less space required for the transverse thrusters. It also allows thrusters to be installed closer to the bow where they are more effective.
Wärtsilä’s extensive experience with propeller design and tunnel optimizations using CFD analysis, ensures an optimal solution when it comes to propulsion performance, efficiency, and the minimization of noise and vibration.
Another benefit of the Wärtsilä WTT-40 is its integrated hydraulics, which save machinery room space and installation and commissioning time at the shipyard.
Innovative ship propulsion systems made by RENK
Military vessels such as patrol boats, corvettes, and frigates looking for “silent running” might well be interested in the Renk Advanced Electric Drive AED. The new drive from the Augsburg, Germany, plant offers a number of special advantages for shipbuilders, says Renk. The propulsion system is a real alternative to the heavy, space consuming electric motors that are rotating at propeller speed.
Modern power electronics allow the use of high-speed motors in combination with an efficient gearbox. The Renk AED combines electric motor and gearbox on one joint frame. Built on soft elastic mounts and equipped with a highly elastic propulsion coupling an incomparably silent operation is possible. The water-jacket of the water-cooled electric motor as well as the double helical reduction gear add to extremely low noise operation.
A modularized lightweight
Thanks to the compact design as well as the low height the preassembled unit is quickly installed with minimum space requirements. Additionally there is a considerable weight advantage. The drive weights around 40% less than a conventional direct drive motor. By comparison, the Renk AED weighs only 23 tons instead of the 35 tons of a direct drive motor of the same power.
Suitable for fixed pitch propellers as well as controllable pitch propellers the drive speed can be flexibly adjusted to the respective propeller requirements. The propulsion systems is built modularly and can be delivered in four sizes from 1.4 to 6 MW. For uses where the requirements are between sizes RENK simply adjusts the capacity of the bigger engine. In this way the complete range of capacities can be covered individually and economically. The motors work with low or mid ranged voltage and are designed –depending on size- for propeller revolutions of 190-450 rev/min.
Investing in new production & testing facilities
Besides pouring millions of dollars into research and development, marine propulsion manufacturers are also investing in new production and testing facilities. Earlier this year, Renk opened one of the largest and most modern test facilities in Europe for gear units at its headquarters in Augsburg. Whether for the shipbuilding, automobile or industrial sector: The multifunctional test facility is especially suitable for the testing of prototypes or special equipment. Renk will not only test its own special gearboxes and propulsion systems, but also those of other propulsion systems or propulsion component manufacturers. The test facility allows for a power capacity of up to 12 MW at 10 revolutions per minute and can take a torque of up to 11 million Nm.
Just this past June, Rolls-Royce Marine unveiled plans for a EURO 57 million plan to upgrade its azimuth thruster plant in Rauma, Finland, and consolidate its thruster assembly and testing to one site.
Rauma produces a wide range of mechanical azimuth thrusters for use on a wide range of applications including semi-submersible drilling rigs and drillships, tugs and offshore vessels. Rauma also produces thrusters for specialist vessels such as icebreakers and polar research ships.
Mikael Makinen, Rolls-Royce, President – Marine, says, “Our azimuth thrusters are one of our most important products, providing mission critical power and propulsion for some of the largest floating objects on the planet. To be able to make this significant investment in Rauma not only prepares us for future growth in this market, but is a vote of confidence in the capability and expertise of our people.””
Azimuthing thrusters rotate through 360 degrees, providing propulsion and maneuverability without the need for a rudder. The largest and most powerful thrusters from Rauma are the ARC type which power icebreakers including the Finnish vessel Fennica. They are among the largest products produced by Rolls-Royce and can each weigh up to 190 tonnes, providing 7.5Mw of power.
Two of the world’s largest floating structures are powered by another range of thrusters produced in Rauma, UUC underwater mountable thrusters:
The heavylift vessel Pioneering Spirit, owned by Allseas, which is used for decommissioning oil platforms, has13 UUC thrusters; and Shell’s Prelude, the world’s first floating LNG production facility, will feature three large UUC thrusters, for position keeping. The thrusters are installed in a novel arrangement that allows them to be removed and maintained within the ship.
The work to transform Rauma will begin immediately and is due for completion in 2020. The investment will include installation of a crane capable of lifting 200 tons, and at least six factory acceptance test rigs. Offices and IT systems will also be refurbished.
JULY 19, 2016 — Rolls-Royce will be presenting new MTU brand propulsion systems designed to meet IMO III and EPA Tier 4 emission regulations for commercial, offshore and military vessels and yachts
JULY 14, 2016 — Madrid, Spain, headquartered SENER reports that its FORAN CAD/CAM system is now in use at Fincantieri Bay Shipbuilding, Sturgeon Bay, WI. SENER last year signed a contract licensing
Over the years, the use of azimuth thruster has changed the way operators do business. The increased maneuverability and efficiency gains allow tug operators to do more with the same installed power. Added maneuverability can also play a role in improving safety during certain operations. With more than 50 years of developing and manufacturing azimuth thrusters, Rolls-Royce has learned a lot about the specific propulsion requirements of different types of ships and floating structures. Working close with the customers has been a key element of the success.
Steerable azimuth thrusters have come a long way since the first one went into service in 1965. With just 80 hp of thrust it was installed on a mud hopper barge in Finland to make it self-propelled. The first azimuth units specifically designed for inland waterway applications were delivered in 1976. They powered a series of three-river push boats built in Holland and are still operating today.
With the aid of modern computer-based design tools and a detailed understanding of hydrodynamics, Rolls-Royce is continuously developing and improving its thruster product range. The current product portfolio covers a power range of 300 to 14,000 hp.
The benefits of Azimuth thrusters on a towboat
With an azimuth thruster the full thrust can be applied in any direction through the full 360 degrees and significantly improve the maneuverability and braking force of the vessel. In performance tests it has been shown that the braking forces produced are nearly 1.5 times those of the conventional towboat, over the whole speed range. This increase in braking force reduces both the distance and the time needed to stop a barge train.
For shallow draft operations, the normal requirement is to fit 2 azimuth units, and it is not unusual to have towboat designs with a triple azimuth thruster propulsion arrangement.
Azimuth thrusters also significantly increase flanking forces, which help operators safely navigate through the most difficult bends of the river. On a conventional towboat, flanking rudders and reverse thrust are normally used to produce the necessary flanking forces. By using azimuth thrusters the transverse force can be maximized and is approximately twice the maximum side force produced by a conventional towboat at all measured speeds, plus there is the benefit of greater braking forces. Maximum flanking forces produced can be up to 4 times that of the conventional towboat with equal braking force.
How Azimuth thruster help in Brazil
Brazil is a country traversed by many rivers, the main one being the Amazon. There are 11 main inland waterways with a total length of some 39,000 miles although only approximately 8,000 miles are regularly used. These waterways are used to transport agricultural commodities such as grain and fertilizer, as well as mineral goods to the coast.
Amaggi Navegação a subsidiary of Amaggi Exportação e Importação Ltda. is one of the operators working in the region who has moved to azimuth thrusters to propel their vessels. They have been operating on these waterways for over 20 years and now have over 30 tugs equipped with azimuth thruster propulsion. Units in their fleet include a range of Rolls-Royce thrusters from our smaller US 105 model to our larger US 255’s.
Amaggi Navegacao operate on the Madeira and Amazones rivers where they are involved in the transportation of grain and soya to and from local processing plants. The move away from conventional towboat design has enabled them to increase the size of barge trains, which is due to increased turning and stopping capacity at full load.
Open propellers are used for the majority of these thruster applications due to the amount of debris in the rivers. The trend outside the Amazon is to fit azimuth thrusters with nozzles and thereby maximize thrust.
The future of Azimuth thrusters
Thruster technology continues to develop. The latest is the introduction of gearless electric drive through the application of permanent magnet (PM) rim drive technology, where the motor surrounds the propeller as a slim ring. The rotor is integral with the propeller and carries a series of permanent magnets. As the magnetic fields interact, the propeller turns. Tunnel thrusters and azimuth thrusters utilizing this technology are now available from Rolls-Royce. The compact and efficient tunnel thruster unit is easy to install and power output is increased by around 25% for the same propeller size. It is a good example of the possibilities that lie ahead.
This technology has now been applied to the azimuth thruster by Rolls-Royce, and the first PM development thrusters rated at 670 hp were installed on the research vessel R/V Gunnerus in March 2015. Nozzle shape can be selected to suit individual applications, but since Gunnerus requires pull for towing trawl and other gear, the nozzle is optimized for bollard pull and speed to match the vessel’s requirements. The installation is compact with only the slip ring unit and the variable frequency steering motors inside the hull.
Before the installation, the vessel had a conventional diesel electric propulsion system consisting of frequency converters, induction motors, gears and shaft with nozzle propeller. Testing to date has demonstrated an improvement in propulsive efficiency and bollard pull with a reduction of air and structure borne noise and vibration.
MAY 20, 2016 —The first of Damen’s new Shoalbuster 3512 class multipurpose workboat, the Noordstrom, was recently handed over to Dutch marine services specialist Van Wijngaarden Marine Services B.V. in the port
APRIL 14, 2016 – Classification society Bureau Veritas has given Approval in Principle (AIP) to the WindFloat Floating Offshore Wind Turbine (FOWT) foundation. Designed by Principle Power, Inc., WindFloat consists of a
With the goal of improving the safety and capability of the marine research industry, Allied Marine Crane, a division of Allied Systems Company, has developed the A-Stern A-Frame. Hydraulically powered, the A-Frame is used to launch and recover trawls, dredges, and ROVs. Its crossbeam rotates freely as it deploys, ensuring that the load—the unit has a 30,000 to 40,000 lb dynamic load capacity—and lighting are properly oriented throughout the entire range of motion.
Last year, the innovative unit was successfully fitted onto the R/V Sikuliaq. The vessel, owned by the National Science Foundation and operated by the University of Alaska Fairbanks School of Fisheries and Ocean Sciences, conducts oceanographic and fisheries related research in polar and sub-polar regions.
Allied says, the A-30 Stern A-Frame’s maintenance position allows crew to access the crossbeam from the deck at a standing height furthering safety during setup and rigging.
The provider also supplied the U.S. Navy’s Office of Naval Research vessels the 238 ft Neil Armstrong and Sally Ride with two sets of crane components. The Neil Armstrong is being operated by the Woods Hole Oceanographic Institution, while the Sally Ride is currently operating for the Scripps Institution of Oceanography at the University of California San Diego.
Under the contract, the company designed and manufactured an identical set of handling equipment for each vessel. The units consisted of a davit; the Stern A-frame; a telescoping knuckle-boom crane; a starboard side handling system and a CTD handling system—both of which extend all the way to the waterline for more stability when loading; a portable telescoping knuckle-boom crane—among the first of its kind in the industry, the unit can be bolted down to a standard UNOLS mounting pattern anywhere on deck and can be removed when its not needed; and two hydraulic power units.
BREAKING INTO A NEW NICHE
Rapp Marine U.S. has taken a huge innovative step forward, developing, what its President Johann Sigurjonsson calls “an ideal tow winch for the market.” Having long been a developer and supplier of electric and hydraulic driven mooring winches, anchor windlasses, capstans, and cranes, Rapp Marine worked closely with Baydelta Navigation Ltd. to develop a towing winch that would be long lasting and dependable for the tug market.
Rapp Marine is supplying a unique, fully electric driven double drum tow winch for a new 110 ft x 40 ft tractor tug operated by Vessel Chartering LLC, a wholly owned division of Baydelta Navigation Ltd. The tug was designed by Seattle-based Jensen Maritime and will be built at JT Marine Shipyard, Vancouver, WA.
The winch, the first fully electric driven tow winch delivered by Rapp Marine, will be able to pull over 75 tons and use pneumatic cylinders in place of hydraulics—to keep fluid off the deck.
According to Rapp Marine, the winch will be driven by a single 100 hp electric motor with the ability to clutch in and out each winch drum. The clutches and brakes will be actuated remotely through either control panels or manually on the winch.
The winch will be primarily controlled in the wheelhouse using Rapp Marine’s Pentagon Tow Control System, which provides for a more efficient and safer operations for towing vessels. The system includes Auto Tensioning, automated haul-in and pay-out settings, in addition to touchscreen displays showing tension and wire length.
Rapp Marine says the winch can store up to 2,500 ft of 2.5 inches of Steel Wire Rope and 90 ft of 3 inch chain on the storage drum. The unit will also include a 10 HP electric “come home” drive. The drive can be used as a back up if the main motor should fail.
SELF-ALIGNING ESCORT WINCH
No stranger to innovation, the man behind the innovative training tug, the BRAtt, Captain Ron Burchett, and his company, Burchett Marine, recently delivered three new scale model tugs to Warsash Maritime Academy in Southampton, UK.
The 8,000 hp, 42m ASD tug models were equipped with the latest winch technology from JonRie InterTech—including a JonRie’s patented self-aligning escort winch.
During testing of the winch at the Academy, the model was able to stop a 44 ft long containership model at a speed of 10 knots. Captain Burchett will return to the Academy later this summer for Round 3 of testing at the 12 to 15 knot range.
The winch, says JonRie, was redesigned to accommodate a new 3-speed Hagglunds motor—this would allow for faster retrieval speeds. The motor will have the capability to free wheel each individual cam ring which comes complete with JonRie’s Render Blocking enabling render speeds to exceed 120 m/min. The tug’s dynamic stability was further enhanced by the righting lever supplied by the winch.
The winch’s hydraulic braking system is rated for 300 tonnes.
Additionally, the winch, explains JonRie’s Brandon Durar, is bolted to its rotating foundation to help prevent distortion to the drive from welding. The winch also contains a load tension read out system and JonRie’s foot control for a hands-free operation.
MACGREGOR WINS CONTRACTS FOR ESL SHIPPING CARRIERS
MacGregor, part of Cargotec, recently won a contract to deliver hatch covers, cranes, deck machinery and steering gear to two 25,600 dwt dual-fueled handysize bulk carriers being built for Finland’s ESL Shipping at China’s Sinotrans & CSC Shipbuilding Industry Cooperation’s Quingshan shipyard.
As part of the deal, MacGregor will provide three K3030-4 mechanical grab cargo cranes with a safe working load of 30 tonnes at 30 m outreach. Additionally, the group will provide the design and key components package for multi folding-type hatch covers (6+6), electrically-driven Hatlapa deck machinery and Porsgrunn steering gear.
Nichols Brothers Boat Builders recently completed sea trials on the second of 10,000 hp oceangoing tugs for Kirby Offshore Marine, the coastal tug and barge arm of Kirby Corporation, Houston, TX. The 136 ft x 44 ft tug, Tina Pyne, will be connected to the 185,000 bbl ocean tank barge 185-02 built by Gunderson Marine, Portland, OR.
Kirby’s newbuild plan also includes two 155,000 bbl/6,000 hp Articulated Tug Barge (ATB) units under construction at Fincantieri Bay Shipbuilding in Sturgeon Bay, WI, as well as two 120 ft x 35 ft, 4,894 hp tugs being built by Nichols Brothers Boat Builders. Each tug will be powered by two Caterpillar 3516C engines, each rated at 2,447 hp at 1,600 rev/min, with Reintjes reduction gears turning two Nautican fixed-pitched propellers with fixed nozzles. The Reintjes gears were supplied by Karl Senner, LLC, Kenner, LA. The tugs will also have two C7.1 Caterpillar generators for electrical service. Selected deck machinery includes one TESD-34 Markey tow winch, one CEW-60 Markey electric capstan, and one Smith Berger Tow Pin.
Kirby Offshore Marine is the largest U.S. operator of coastal tank barges that provide regional distribution of refined petroleum products, black oil and crude oil. Kirby grew its coastal marine transportation business through the acquisition of K-Sea Transportation Partners L.P. back in 2011 in a transaction valued at about $604 million. At that time, Kirby acquired 58 tank barges (only 54 were double hull) with a capacity of 3.8 million barrels and 63 tugs.
Already the operator of the largest inland tank barges and towboats, Kirby Corporation will grow further with the purchase of Seacor Holdings Inc.’s inland tank barge fleet for about $88 million in cash.
Under the terms of the deal struck last month, Kirby will acquire 27 inland 30,000 bbl tank barges and 13 inland towboats, plus one 30,000 bbl tank barge and one towboat currently under construction. As part of the agreement, Kirby will transfer to Seacor the ownership of one Florida-based ship-docking tugboat.
Kirby Inland Marine currently has 898 active inland tank barges and 243 towboats, with a total carrying capacity of 17.9 million barrels. The primary cargoes transported by this fleet are chemicals, petrochemical feedstocks, gasoline additives, refined petroleum products, liquid fertilizer, black oil and pressurized products.
Kirby President and CEO David Grzebinski, says “Operating primarily in the refined products trade, these assets will be complementary to our existing fleet and will allow us to continue to enhance customer service.”
TRIPLE-SCREW BOATS FOR MID-RIVER
Over the years, Rodriguez Shipbuilding, Inc.’s triple-screw towboats have won a following operating in the shallow waters where the Mississippi River meets the Gulf of Mexico. These Lugger-type vessels are designed with a distinctive aft-cabin.
Mid-River Terminals of Osceola, AR, recently took delivery of a new design towboat from Rodriguez Shipbuilding, Coden, AL. With a conventional forward-house pusher configuration, the new 70 ft x 30 ft MV/ Dianna Lynn uses the same propulsion as the Lugger tugs. This is composed of three in-line six-cylinder Cummins QSK 19 engines, each delivering 660 hp. Each engine turns a 66-inch stainless steel propeller through ZF gears with 6:1 reduction ratio. The combination gives the 1,980 hp towboat an eight-foot operating draft.
Fitted with large windows, the wheelhouse has a full 360-degree view and is set atop two accommodation decks and a half deck that also serves for bridge electronics support. This gives the towboat a 31-foot high eye-level, with full tanks, for working high barges.
Steering and flanking rudders are controlled by wheelhouse levers with mechanical shafts through the houses and connected to the hydraulic actuator valves in the upper engine room.
A set of push knees and deck winches with cheek blocks facilitates barge work. A pair of 55 kW gensets meets the boat’s electrical requirements.
Zero discharge tanks, built integral to the hull, provide storage for treated sewage and all drains. A separate tank handles waste oil.
The M/V Dianna Lynn is the fourth boat in the Mid-River Terminal fleet, all of which are Cummins powered. Owner Rick Ellis said, “We wanted the three engines for redundancy so that even if we loose an engine we still have over 1,200 horsepower.”
The new boat will be primarily involved in fleeting and harbor work, “Rodriguez did a great job and it is a great handling boat,” Ellis added.
BOUCHARD, MORAN EXPANDING FLEETS
As we highlighted last month, Bouchard Transportation’s multi-million-dollar newbuild program is winding down. The Melville, NY, owner is completing the construction of two new 6,000 hp, 310 ft x 38 ft Intercon tugs at VT Halter Marine, Pascagoula, MS. The tugs Morton S. Bouchard Jr. and Fredrick E. Bouchard will be connected to the B. No. 210 and B. No. 220. The two tank barges were the first double hull tank barges built by Bouchard,. Both were built as wire barges, but following their conversion and stretch at Bollinger Shipyards, Inc., both will be Intercon, flat deck double hulls capable of carrying 110,000 bbl of oil.
Moran Towing, New Canaan, CT, expects to take delivery shortly of a 5,300 hp/110,000 bbl ATB unit from Fincantieri Bay Shipbuilding. The Sturgeon Bay, WI, has another 8,000hp/155,000 bbl ATB unit under construction for Plains All American Pipeline, with an option for a second unit, and signed a hotly contested order for another 8,000 hp/185,000 for another earlier last month. That contract includes an option for another.
The new barge will have a capacity of 185,000-barrels with dimensions of 578 feet by 78 feet. The tug will be an 8.000-HP unit equipped with Tier 4 engines—believed to be GE Marine—to meet the latest EPA emission standards.
When complete, the ATB will operate on the U.S. East Coast and Gulf of Mexico.
“We are pleased to have this opportunity,” said Francesco Valente, FMG President and CEO. “This new contract marks an additional expansion of our product portfolio, confirms our ability to win business with new customers in a very competitive market and further consolidates our presence and reach in the U.S. market.”
“This award increases our pipeline of new construction to 10 vessels and provides additional stability to our business,” said FBS Vice-President and General Manager, Todd Thayse. “We are grateful for the confidence that our customers continue to place in our reputation for quality and the strong shipbuilding skills of our workforce.”
Conrad Shipyards, Morgan City, LA, meanwhile, is building the 80,000 bbl ATB unit for John W. Stone, as well as two ATB tugs for Harley Marine Services, Seattle, WA. Conrad Orange Shipyard in Orange, TX, recently delivered the 35,000 bbl Double Skin 315 to Vane Brothers Company. That barge was towed to New York by the Elizabeth Anne, the first in a series of eight 4,200 hp tugs being built by St. Johns Ship Building, Palatka, FL.
Designed by Frank Basile, P.E. of Entech Designs, LLC, the Elizabeth Anne Class tugboat is a close cousin to Vane’s Basile-designed Patapsco Class tugboats, 15 of which were produced between 2004 and 2009. Measuring 100 feet long and 34 feet wide, with a hull depth of 15 feet, the model-bow Elizabeth Anne utilizes two Caterpillar 3516 Tier 3 engines, each generating 2,100 hhp at 1,600 rev/min. Two John Deere PowerTech 4045, 99 kW generators deliver service power to the boat, while a third John Deere 4045 teamed with an Allison transmission drives the chain-driven INTERCON DD200 towing winch.
ROBERT ALLAN’S LATEST
Over the years, world renowned naval architectural and marine engineering firm Robert Allan Ltd. Has successfully teamed with shipyards around the world to bring new innovative tug designs to the market. Its latest is the VectRA 3000 Class Tug, a high performance VSP Tractor tug designed by Robert Allan Ltd in close collaboration with Turkish ship builder Sanmar and Voith Turbo Propulsion. The tug is designed for maximum efficiency in the performance of towing, harbor ship-handling and escorting of large ships. Performance has been verified with extensive model tests at the commencement of the design cycle. The unique propulsion arrangement features high-speed diesel engines connected to the Voith units via reduction gearboxes with integral clutches. With a bollard pull of 70 tonnes, the VectRA 3000 form can generate escort steering forces in excess of 100 tonnes. Additionally, the design has fire-fighting and oil recovery capabilities and is fully MLC compliant.
The VectRA 3000 has been designed exclusively for Sanmar to offer as one of its highly successful stable of progressive tugboats for the world market.
The first vessel in the series, the M/T Ares, built for Italian tugowner Tripmare SpA, was successfully launched at Sanmar’s new Altinova advanced shipbuilding facility this past February.
The tug has an overall length of 30.25 m, beam of 13m, depth of 5.1m, and design draft of 6.1m.
The vessels are built and classed to the following ABS notation: ✠ A1 Towing Vessel, Escort Vessel, ✠ AMS, Unrestricted Service, UWILD, HAB (WB), ABCU Fire-Fighting Vessel Class 1 Oil Spill Recovery – Capability Class 2 (>60° C) (OSR – C2).
Rather uniquely for a VSP installation, the propulsion drivetrain comprises two Cat 3516C high-speed diesel engines, each rated 2,525 kW at 1,800 rev/min, and driving Voith 32R5EC/265-2 cycloidal propellers. The engines are connected to the Voith drives through a pair of Reintjes WAF 863 gearboxes and Vulkan composite shafts, rather than using the more traditional turbo coupling. This combination is smaller, lighter and less costly than the traditional medium speed drive system. The electrical plant consists of two identical diesel gensets, each with a rated output of 86 ekW.
Crew accommodations are all located on the main deck level for optimal crew comfort. There are 4 single crew cabins plus 1 double crew cabin, each with an en-suite bathroom. A comfortable lounge/mess area and galley facilities are also in the deckhouse, with galley stores and laundry room located below the main deck forward.
All towing, ship handling, and escort work is performed using a double drum escort winch and escort rated staple fitted on the aft deck. One drum can store 710 meters of steel wire line, while the other stores 150 meters of synthetic towline. For increased operational flexibility radial type tow hooks are installed on the main deck forward and aft.
As in a traditional tractor configuration, the stern is the working end of the tug, and as such features heavy-duty cylindrical fendering with a course of ‘W’ fenders below. Hollow ‘D’ fenders protect the sheer lines and tie neatly into the ‘W’ fenders at the bow.
The wheelhouse is designed for excellent 360-degree visibility and includes overhead windows. The split type console is biased aft to ensure unobstructed visibility of the working deck (including the winch, staple, bulwarks and fenders) during operations.
CARGILL’s PUSHBOATS FOR THE AMAZON
In Brazil, the construction of a fleet of Robert Allan Ltd.-designed pushboats and barges for Cargill Transportation is nearing completion. To be used for transporting grain products on the Amazon River system, the fleet includes two shallow-draft RApide 2800-Z2 class pushboats built at INACE in Fortaleza, Brazil and 20 hopper barges built at Rio Maguari in Belem, Brazil.
Each of the two new RApide 2800-Z2 Class pushboats are 28m x 10.5m, with a minimum operating draft of 2.2m and normal operating draft of 2.5m. The two sister vessels, the Cargill Cachara and Cargill Tucunare, are designed to push barge convoys on the Amazon River system.
During the early phases of design, extensive CFD simulations were undertaken to optimize the pushboat’s hull shape to minimize total convoy resistance.
This work was completed in conjunction with extensive logistics modeling of the transportation system to optimize the selection of vessels for the desired route and to analyze operational drafts and cargo throughput at various river levels.
The pushboats were designed to ABS and Brazilian NORMAM-02 requirements and are outfitted to the highest standards.
The wheelhouse is designed for maximum all-round visibility with a split forward control station providing maximum visibility to the foredeck working area of the tug as well as to the convoy of barges ahead. Accommodation for up to 13 people is provided onboard and a large galley and mess is provided on the main deck.
The deckhouse extends aft over the main propulsion components, which comprise a pair of Caterpillar 3512B diesel engines, driving Schottel SRP 550 Z-drive units. The drives are fitted in tunnels designed to optimize flow while reducing draft. Two identical Caterpillar diesel gensets are provided in the vessel’s auxiliary machinery space located below the main deck.
The corresponding 61m x 15m box and rake barges were designed by Robert Allan Ltd. to ABS River Rule requirements. Additional extensive FEA analysis of the structure was performed in order to optimize the design for minimum steel weight while ensuring long service life during river operations. Sliding aluminum hatch covers have been supplied to ensure the cargo stays dry at all times.