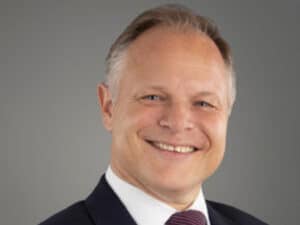
Subsea Industries grows its products family
Written by Nick BlenkeyDECEMBER 3, 2018 — Since launching its durable, non-toxic hard hull coating system Ecospeed back in 2002, Antwerp, Belgium, headquartered Subsea Industries has added a number of other products to its line-up.
The first of these, Ecoshield, is an enhanced version of Ecospeed launched in 2013 after years of testing small but significant variations of the Ecospeed formula, initially under the name Ecospeed Strong.
Ecoshield is designed to protect rudders and other underwater running gear against the cavitation phenomenon: against pitting, corrosion and erosion.
Subsea Industries says that a constantly growing number of customers have vessels sailing with the Ecoshield coating system on their rudders for up to ten years and counting and that when they come into dry dock, the coating is always in very good shape. Since 2013, for example, Ecoshield has been applied to the rudders and thruster nozzles of ten vessels owned by Greek ship owner Pleiades Shipping Agents. Some of these vessels have since drydocked but, as their rudders and nozzles experienced zero cavitation damage, they did not need to be recoated.
Ecoshield is not only used on rudders, but also on thrusters, thruster tunnels, nozzles and other running gear. Subsea Industries says it is also in communication with OEMs to include Ecoshield in the newbuild plans of their products, allowing them to offer their customers a complete package with lasting protection.
Ecofix
Ecofix is used for filling and building up a corroded and pitted steel surface to its original form prior to coating it with Ecoshield. Subsea Industries says that Ecofix is as tough as the steel itself. It is machinable and can be used to repair most pitting or corrosion damage on rudders, stabilizer fins, thrusters and other underwater gear.
When a rudder or other piece of underwater ship gear has not been properly protected, the surface will become corroded. Cavitation damage can cause severe pitting. The steel needs to be restored to its original shape with a smooth surface prior to recoating.
This is where Ecofix comes in. It is a superior, tested and proven filler. As it uses the same basic ingredients as Ecoshield, the coating can be applied just one hour after the filler. The bonding and hardness are extraordinary. It is an effective alternative to metal facing or very expensive alternative fillers and is fully compatible with other Subsea Industries coatings.
Ecolock
Ecolock is used on stationary offshore units that are designed to stay on location for 15, 20 and even up to 30 years. Hull integrity and corrosion protection is a major thing.
The main benefit of the coating system is corrosion protection and the possibility of cleaning the system to meet Class demands for an underwater inspection of such offshore units twice every five years to see if the hull is in good shape. If the hull is cleaned on a frequent basis, say every two years, says Subsea Industries “this offers no problems at all.”
Subsea Industries standard warranty is ten years, but for Ecolock this can be extended to 15 or 20 years, depending on the number of layers. applied.
Major offshore projects completed by Subsea Industries include two for Exmar NV, including the world’s first floating LNG liquefaction barge, the Caribbean FLNG, in 2013. The main reason for choosing Ecolock was to protect the underwater hull from corrosion for at least 15 years without having to drydock or repair or replace the hull coating. Another key factor in choosing the hull coating system was the need for a clean, environmentally safe hull to facilitate the required class inspections.
Another Ecolock project was a unit planned for deployment in Colombia where there is a major fishing industry and where the owner and the local authorities wanted to be absolutely sure that no toxic elements would be leaching into the aquatic environment either during regular activity or during cleaning.
Ecolast
The latest product to join the Subsea Industries family is Ecolast, launched in 2016. This coating is ultraviolet (UV) light resistant and preserves its color while at the same time offering the corrosion and abrasion protection our coatings are known for.
Regular coatings will quickly lose their original color when exposed to the ultraviolet radiation present in sunlight. This is problematic when colorfastness is required, as is the case in for example offshore wind farms.
Ecolast is highly resistant against salt, ultraviolet radiation, waves and even ice. Mechanical damage to the coated surface is minimized. This is especially important for (semi-)submerged structures such as wind turbines that are located in splash or tidal zones.
Like all other coatings systems in the Subsea Industries family, Ecolast is also unaffected by corrosion. As a result no repaint is required once the coating has been applied.
Leave a Reply
You must be logged in to post a comment.