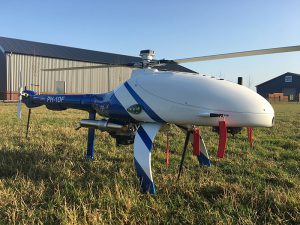
Martek Marine to play major role in EMSA drone project
MARCH 17, 2017 — Rotherham, U.K., headquartered Martek Marine is to play a key role in one of the world’s maritime drone projects. The company has been awarded a two year contract
MARCH 17, 2017 — Rotherham, U.K., headquartered Martek Marine is to play a key role in one of the world’s maritime drone projects. The company has been awarded a two year contract
DECEMBER 20, 2016 —A statement posted on China’s Ministry of National Defense said Tuesday that China has “handed over the U.S. underwater drone it captured in its waters to the United States,”
SEPTEMBER 18, 2016 — The Danish Maritime Authority now has its first certified drone pilot and plans to now use a drone as a supplementary means of inspecting its lighthouses. The authority
JUNE 15, 2016 — The Gard P&I Club reports that a vessel entered with the club was recently detained following the launch of a drone to photograph the vessel proceeding through the
MARCH 11, 2016—The Maersk Group envisions that one day it will be able to use drones for vessel inspections, firefighting, surveillance for navigation and anti-piracy operations, and to deliver vital goods to
“We have been looking at ways we could help our customers by accelerating the survey process,” says Cezary Galinski, Manager of the DNV GL – Maritime classification flying squad based in Gdansk. “Camera equipped drones are now much more widely available and affordable, and by using them for a first screening we can identify areas that require closer inspection quickly and without extensive staging, which can be both costly and time-consuming.”
Using drones to visually check the condition of remote structural components has the potential to significantly reduce survey times and staging costs, while at the same time improving safety for the surveyors.
The tests used a camera-equipped drone to visually evaluate structural components through video streamed to a tablet. One surveyor operated the drone, while a second checked the video feed in real time. The stream was also recorded for review and documentation purposes.
Equipped with a powerful headlight, the drone was able to produce a video of sufficient quality for initial inspection purposes. In the event any damage is detected, a traditional close-up survey may still be required.
“We used a modified off-the-shelf drone for our tests,” says Mr. Galinski. “Because there are currently no drones formally certified as explosion-proof commercially available, we performed a risk assessment. Of course, before the drone operation started, we also ensured that the cargo tank was gas-free and certified for safe entry.”
“Our next step is to work with a more advanced tailor-made drone in early 2016,” says Mr. Galinski. “We are also developing a special guideline for performing drone-based surveys. This could open the way to remote or even autonomous inspections being carried out as part of our survey scheme in the near future.”
DNV GL has a longstanding R&D program working on developing advanced inspection technologies, including the IRIS system which can automatically associate photos onboard a ship with a 3D model of the vessel’s structure.
“Using a drone in combination with a system like IRIS could be very beneficial to our customers,” says Dr. Pierre C. Sames, Director of Group Technology and Research. “We have already demonstrated the ability to place images within a 3D model and furthermore to assess the individual findings. These are the first steps towards an automated survey process which might include using a drone to make the initial survey, taking the images generated and then running them through an algorithm to determine the hull condition.”
Drone technology is also finding applications in the maritime industry for the same reasons.
“We see opportunities to use robotics to reduce the danger to crews posed by riskier tug operations, and to reduce costs in some cases,” says Mike Fitzpatrick, President & CEO of Vancouver-based naval architectural firm Robert Allan Ltd. “Control and digital communication technologies developed for drones used in other sectors have reached the point where its transfer to our industry is completely feasible, and is perhaps overdue. These technologies have been used in smaller autonomous surface vessels (ASVs), autonomous mine trucks, autonomous underwater vehicles (AUVs) and aerial drones for years.”
Robert Allan Ltd. (RAL) has just unveiled an autonomous tug concept called the RAmora. The first in the company’s TOWBoT (Tele-Operated Workboat or Tug) series, the RAmora 2400 is a versatile towing platform designed primarily for ship assist and berthing operations. With a bollard pull of 55 tonnes, the RAmora 2400 features a hybrid propulsion system and ample battery storage capacity to enable extended operation even in potentially hazardous environments such as LNG terminals or fire-fighting situations.
The RAmora is operated remotely by a captain on a command tug using a console equipped with live video and other positioning information. “It is also possible,” explains Fitzpatrick, “for the RAmora captain to operate RAmora away from the console by a bellypack controller when in close visual range.”
The control system design was developed in partnership with International Submarine Engineering of Port Coquitlam, Canada, and is derived from proven remotely operated vehicle, autonomous underwater vehicle and surface vessel applications.
RAmora is fitted with Voith Schneider Propeller (VSP) drives arranged in a fore/aft configuration and its hull form, designed for high stability and good seakeeping performance in waves, is the product of extensive development work including CFD and towing tank testing. Yet, being a TOWBoT with no need for a conventional wheelhouse, crew accommodations, domestic systems or lifesaving equipment, RAmora is simpler and more compact than any conventional tug of comparable performance.
Other features incorporated into the RAmora include off-ship fire-fighting (fi-fi) capability classed to “Fi-Fi 1”, two 1,200 m³/hr fire monitors supplied by electrically-driven fire-fighting pumps, a crane boom that can be optionally fitted with a smaller 600 m³/hr fire monitor and camera.
RAmora can be used for ship handling operations that can put crew at risk, for operations at terminals where ship handling may be required in emergency situations in hazardous environments, or as a fire fighting asset that can work in close proximity to a toxic fire, or in a restricted space, for extended periods with no risk to crews.
But don’t expect the RAmora to appear in the market overnight. “While the core control and communication technologies are mature,” cautions Fitzpatrick, “there is a lot of work to be done to get to the point where industry, class and regulatory authorities are completely satisfied that safety and reliability meet or exceed what is presently achieved with conventional tugs for the type of ship handling operations that RAmora is intended for. That process could take several years, and we need to be realistic about that. On the other hand, building a prototype RAmora could be done in as little as one to two years since there are no major technological obstacles. We see it as more of an exercise in integrating existing technologies. In many respects, without the normal outfitting required for a crewed tug, RAmora is simpler to build and has considerably fewer systems.”
SEPTEMBER 27, 2015 —Jan Andersen, one of Danish shipowner DS Norden’s three U.S.-based port captains, has started using a drone fitted with a small video camera to speed up cargo hold inspections.
SEPTEMBER 2, 2015 — Poland’s Remontowa shipyard recently used a drone to inspect internal spaces in a 51,747 dwt chemical/product tanker. The ship, the U.K.-flagged, LR-classed CPO Japan is owned by Hamburg,