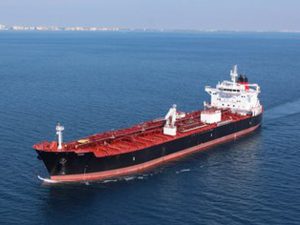
Crowley takes delivery of second LNG ready tanker
The shipyard is the sole operating subsidiary of Oslo-listed Philly Shipyard ASA, which is majority-owned by Converto Capital Fund, which in turn is majority-owned by Aker ASA.
“We are proud to deliver another ship to Crowley and the first under our new name, Philly Shipyard. The Texas, like our 21 previously delivered vessels, continues the long tradition of men and women building quality vessels in Philadelphia,” said Philly Shipyard President and CEO Steinar Nerbovik. “As we continue to build the eight ships in our backlog, we are always looking for more skilled men and women to add to our team.”
The 50,000 dwt, 330,000-barrel-capacity Texas and sister ship Ohio, which was delivered to Crowley in October, are first ever tankers to receive ABS(ABS) LNG-Ready Level 1 approval, meaning Crowley has the option to convert the tanker to liquefied natural gas (LNG) fueled propulsion in the future. The remaining two product tankers being built by Philly Shipyards for Crowley have planned deliveries from the shipbuilder in 2016.
“We are excited to close out 2015 with the addition of this technologically advanced vessel to our fleet of U.S.-coastwise product tankers,” said Rob Grune, Crowley’s senior vice president and general manager, petroleum and chemical transportation. “We constantly strive for ways to enhance the services we provide to our chemical and petroleum customers. The introduction of vessels like Ohio and Texas, with their advanced technology and environmentally friendly fuel options, prove that we are innovating the industry and we are doing it with American built, Jones Act vessels.”
The new 50,000 dwt product tankers are based on a proven Hyundai Mipo Dockyards (HMD) design which incorporates numerous fuel efficiency features, flexible cargo capability, and meets the latest regulatory requirements. The vessel is 600 feet long and is capable of carrying crude oil or refined petroleum products.
Crowley’s Seattle-based, naval architecture and marine engineering subsidiary Jensen Maritime is providing construction management services for the product tankers. Jensen now has an on-site office and personnel at the Philadelphia shipyard to ensure strong working relationships with shipyard staff and a seamless construction and delivery program.