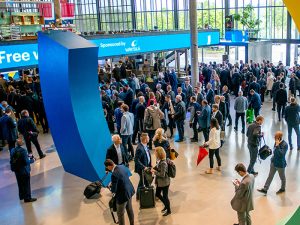
No Nor-Shipping in 2021
There will be no Nor-Shipping event in Norway this June. The organizers have taken the decision to postpone the exhibition and its associated activity program, pushing the event back to January 10-13,
There will be no Nor-Shipping event in Norway this June. The organizers have taken the decision to postpone the exhibition and its associated activity program, pushing the event back to January 10-13,
SEPTEMBER 20, 2018 — Turkey’s Tersan Shipyard recently signed contracts with Norway’s Havila Kystruten AS (Havila) to construct two LNG hybrid battery coastal passenger vessels that will enter operation in Norway’s coastal
JULY 4, 2018 — Nexans Subsea Operations recently signed a contract with Norway’s Ulstein Verft to build a DP3 149.9m x 31m cable laying vessel. Designed by Skipteknisk, Alesund, Norway, the ST-297
MAY 4, 2018 — For years, Norway has been actively working through the International Maritime Organization (IMO) to limit greenhouse gas (GHG) emissions from international shipping and, at home, has pursued a
JUNE 2, 2017—On the day when President Trump said the United States would pull out of the Paris Climate Accord, Norway’s Minister of Trade and Industry Monica Maeland was busy unveiling the
“Orders are drying up. We are faced with an unimaginable situation at which our dock may soon be empty,” wrote Choi Kil Seon, Chairman of the world’s largest shipbuilder, Hyundai Heavy Industries, in a letter to employees this past March. Complacency had set in during the boom years of the 2000’s, he said, despite strenuous efforts to compete with Chinese shipbuilders.
His stark warning has been echoed around shipbuilding halls across Asia. Chinese shipbuilding is undergoing massive retrenchment with the closure of many second-tier shipyards and massive state aid for those still in business. Meanwhile, Japanese shipyards fear a slump that could prove worse than the crash that followed the 2008 financial crisis. Shipyard executives fear the worst as current projects come to an end and have no pipeline of business to speak of.
About 5,000 miles away, workers in the high-tech Kleven Shipyard just outside Ulsteinvik on Norway’s west coast may or may not be aware that their counterparts in Asia are staring into the abyss. And they would certainly not recognize the term complacency in any aspect of shipyard operation.
A combination of effective marketing, chunky investment in automation and robotics, clever use of the country’s export credit arrangements, and close cooperation with Rolls-Royce ship designers who work just across the fjord, has enabled the family-owned shipyard to build up an order book now potentially worth more than $1.8 billion.
Early in July, the yard announced its latest contract for the construction of two—with an option for an additional two—ice-strengthened expedition ships designed by Rolls-Royce (rendering pictured at right) for Norway’s Hurdigruten. Hurdigruten operates a fleet of cargo and passenger vessels around the country’s 15,700-mile coast. The order, worth billions of Norwegian krone, is the largest in Hurdigruten’s history and is a major coup for the shipyard and Rolls-Royce which, in addition to vessel design, will supply about $15 million of equipment for each ship.
Together with the yard’s existing 16-ship order book, Kleven now has work for the rest of this decade. Ships under construction include six anchor handlers for Maersk Offshore, four high-tech stern trawlers of Rolls-Royce design for German, French and Spanish owners, the world’s most advanced cable layer with the highest DP3 position-keeping for ABB, two Rolls-Royce design live fish carriers, a deep-sea mining vessel for de Beers, and two luxury megayachts for a New Zealand entrepreneur. Talk about a diverse order book.
How has the yard been able to buck the global trend, particularly in one of the most expensive parts of the world? Certainly the Norwegian Export Credit Guarantee Agency has played an important role by making attractive financing terms available for foreign owners and vessels to be deployed overseas. But the yard’s management has spent almost $60 million on upgrading yard facilities over the past five years.
The robotic welding process, using lasers, continues to evolve, with a vision control system recently installed and developed by the University of Trondheim. The automated process allows welding rates of more than 300 feet per hour transforming manual rates of a typical eight feet per hour. “This is how we believe we can stay ahead of our competition and be competitive on price,” said a yard representative recently.
However, while the Kleven story may be exceptional—other yards in Norway’s usually bustling Sunmøre region are wrestling the challenge of an unprecedented offshore downturn—the design and shipbuilding innovation evident in northern Europe still facilitates construction of some of the world’s most sophisticated vessels.
In a radius of just a few miles from Kleven, there are several Vard yards, now owned by Fincantieri, the Havyard and across the fjord, next door to Rolls-Royce is Ulstein. Between them, these shipbuilders have completed some of the most sophisticated vessels ever built. They include the latest generation seismic survey ships, light well intervention vessels, offshore construction vessels and ultra-sophisticated cable layers.
Norway is not alone, however, in blazing a shipbuilding innovation trail. Finnish ship designers have unmatched expertise in ice-class design and construction, likely to be in heavy demand as warming seas enable navigation through the Northern Sea Route. Presumably with this in mind, Russia’s United Shipbuilding Corporation completed the acquisition of what is now called Arctech Helsinki Shipyards at the end of 2014.
Sited adjacent to the ice model test basin now known as Aker Arctic Technology Inc, the Helsinki shipyard has undergone various changes in ownership over the years, but has always focused primarily on ice-class design and construction. More than 500 ships have been built since it was established 151 years ago and more than 60% of the icebreakers now in operation around the world were built there.
The Helsinki yard has pioneered a range of ice-class innovations over the years, often with others. These include ‘double-acting’ vessels, which can break ice by bow or stern, azimuthing propulsion for ice operation, heeling and air-bubbling systems, shallow-draft icebreaker designs for inland waterways and coastal seas, and nuclear-powered icebreakers.
The shipyard continues to innovate. In 2014, the shipyard delivered the first “oblique icebreaker” to Russia’s Federal Agency of Sea and River Transport. The Baltika has an asymmetric hull and three azimuthing thrusters with a total installed power of 9 MW. She can break ice ahead, astern or sideways and can open up a 160-foot channel in two-foot thick ice.
The shipyard’s most recent delivery is the first dual-fuelled icebreaker to be powered by LNG and diesel. The Polaris, with a bollard pull of 200 tonnes, is powered by two 6.5 MW stern Azipods and one 6 MW unit, all supplied by power and automation company ABB. She is the Finnish Transportation Agency’s eighth icebreaker.
Polaris will be powered by Wärtsilä’s dual-fuel engines capable of operating on both liquefied natural gas (LNG) and low sulfur diesel fuel. Wärtsilä’s scope of supply consists of one 8-cylinder Wärtsilä 20DF, two 9-cylinder Wärtsilä 34DF, and two 12-cylinder Wärtsilä 34DF engine. Additionally, Wärtsilä secured a five years maintenance agreement for all engines and generators including spare parts, remote online support, CBM monitoring and training services.
The EURO 123 million ($136 million) vessel, classed by Lloyd’s Register, also has an emergency response and oil spill recovery capability and completed sea trials successfully in June. Her 800 m3 of LNG storage will provide an endurance of up to 30 days when operating in the Gulf of Bothnia.
Norway has led the way in the development of gas-powered ships and Rolls-Royce has been one of the pioneers. Designed by NSK Ship Design, the gas-powered cargo ship M/S Høydal features a Bergen gas engine, Promas combined rudder and propeller, and a hybrid shaft generator from Rolls-Royce. The ship was built at Tersan Shipyard in Turkey and delivered to NSK Shipping. The DNV GL class Høydal transport fish feed manufactured by BioMar to the numerous salmon and trout farms of northern Norway.
Boaty McBoatface lives on
Rolls-Royce engineers are also designing the 128m polar research vessel RRS Sir David Attenborough, which will be built at Cammell Laird’s site in Birkenhead on Merseyside, England. As you might recall, the project drew worldwide attention and almost blew up the internet when the public overwhelmingly chose the name “Boaty McBoatface” for the £200 million vessel during a “Name Our Ship” campaign held by Britain’s Natural Environmental Research Council. The council saved face—pun somewhat intended—by choosing the fourth most popular name submitted, “Sir David Attenborough,” after the famous British naturalist.
NERC says a remotely operated vehicle used by the Sir David Attenborough in its research will be named Boaty McBoatface instead.
The project is the biggest commercial shipbuilding contract in Britain and one of the biggest for more than a generation. When delivered in 2019, the Sir David Attenborough will carry out oceanographic and other scientific work in both the Antarctic and Arctic as well as transporting supplies to Antarctic research stations.
The research vessel will be Polar Code 4 ice class, with an endurance for voyages up to 19,000 nautical miles, space for a total of 90 people and a large cargo capacity. The vessel is also designed to generate very low levels of underwater radiated noise and minimize the risk of pollution. Onboard laboratories will allow the prompt analysis of samples.
As part of its £30 million contract, Rolls-Royce will supply the diesel electric propulsion system which will include new Bergen B33:45 engines, two nine-cylinder and two six-cylinder engines, and two 4.5m diameter Rolls-Royce Controllable Pitch Propellers (CPP). The powerful, efficient and compact engines and strong propellers will be able to push the vessel through approximately one meter thick level ice with extremely low underwater radiated noise, avoiding interference with survey equipment or disturbing marine mammals and fish shoals.
According to Jørn Heltne, Rolls-Royce, Senior Vice President for Sales in Ship Design & Systems, Rolls-Royce will also deliver automation and control systems, including its Dynamic Positioning system and Unified Bridge.
Also, Rolls-Royce deck handling systems will support a wide range of tasks, such as towing scientific equipment for subsea acoustic survey equipment using up to 12,000m of wire, or deploying equipment over the side or through a moonpool to collect seawater and seabed samples at depths of up to 9,000m.
OEMs capitalize on new era of ‘smart shipping’
Rapid advances in satcom technology is finally enabling shipping to go digital and make the most of ship-shore connections. While a handful of companies have wired up their ships over the last few years—notably the world’s largest container line, Maersk, high-throughput broadband now facilitates 24/7 connectivity and introduces a new era of remote monitoring, diagnostics, predictive maintenance and shore-side support.
Other transport modes have been using these technologies for some time, but satellite coverage across the world’s oceans has remained a challenge. Many thousands of unconnected ships still provide manually prepared noon reports for managers ashore, an asset monitoring procedure which some from outside shipping can scarcely believe.
Rolls-Royce, through its TotalCare service, has been monitoring the performance of thousands of jet engines for years. Instead of signing service agreements and charging customers for call-outs, spare parts and attendance at unexpected breakdowns, the company’s “power-by-the-hour” concept is aimed at keeping planes in the air and avoiding any downtime.
Earlier this year, London-listed Inmarsat launched Fleet Xpress, a high-throughput broadband service available through its Global Xpress network on its latest satellite constellation. As well as enabling a completely new range of ship-shore connections including internet, email, social media and video conferencing, third party app providers can procure bandwidth on Fleet Xpress to provide their own “smart” services (see accompanying feature, “Fleet Xpress brings ‘smart’ ship tipping point,” for more details).
Systems similar to the Rolls-Royce TotalCare service are now being introduced in shipping. Wärtsilä recently paid EURO 43 million ($47.5 million) for Finnish energy management and analytics firm Eniram which has sensor and analytics equipment installed on about 270 vessels and a turnover of EURO 10 million ($11 million) in 2015. The Helsinki-based firm has established a sound track record in raising vessel efficiency by optimizing trim, engine load and speed, thereby saving fuel and cutting emissions.
The acquisition will strengthen the company’s recently launched Wärtsilä Genius service in which key components are monitored in real time, exceptions noted, and maintenance procedures optimized. A virtual service engineer will also be available as part of the service and the company plans to make more details available at this year’s SMM in September.
Competitor ABB is preparing to open its fourth “Integrated Operations Center” in the United States later this year, probably in Houston. The company has already opened a facility for its offshore clients in Billingstad, Norway, and two similar centers for shipping customers in Helsinki and Singapore.
A fifth center is also likely to be set up in China. By mid-year, ABB had established real-time connections between the centers and clients’ ships, enabling ABB personnel to track performance and provide shore-side support if necessary. Meanwhile Rolls-Royce Marine is also in the process of setting up connections to monitor its equipment in operation at sea.
Following a successful remote monitoring pilot project, Radio Holland recently struck a deal with China Navigation Company for the maintenance of its navcom equipment onboard the owner’s newbuild, multipurpose vessels and bulk carriers.
“The maintenance agreement with Radio Holland has been designed to dovetail with the end of the warranty period for our newbuildings,” says Martin Cresswell, Fleet Director, China Navigation Co. Pte., “and is a continuation of the excellent cooperation that we have built over the last few years. The agreement incorporates remote monitoring, which we believe will significantly reduce out of service periods, increasing operational safety.”
MAN Diesel’s largest two-stroke engine yet
Just this past June, China State Shipbuilding Corporation (CSSC) acquired Wärtsilä’s 30% shareholding in Winterthur Gas & Diesel Ltd. (WinGD). WinGD, Winterthur, Switzerland, will continue as an independent, international company to develop and innovate its two-stroke low-speed marine engine portfolio serving all merchant markets and customers worldwide.
WinGD was one of the earliest exponents of diesel technology. It started the development of large internal combustion engines in 1898 under the “Sulzer” name.
“With the transfer of the shares in WinGD from Wärtsilä Cooperation to CSSC, we will be able to establish even closer cooperation with one of the leading global shipbuilding conglomerate CSSC enabling us to accelerate the development of reliable, efficient and innovative two-stroke low-speed engines meeting the market demands of merchant shipping of the future. WinGD will continue to work with the Wärtsilä Corporation Service Network to serve our customers for after-sales support,” says Martin Wernli, CEO of WinGD.
In other news in the two-stroke diesels, this past May, the 19,437-TEU MSC Jade was delivered by Korea’s Daewoo Shipbuilding & Marine Engineering (DSME) with what is the largest and most powerful engine yet from MAN Diesel & Turbo. Built by Doosan Engine in Korea under license from MAN Diesel & Turbo, the MAN B&W 11G95ME-C9.5 two-stroke engine is rated at an impressive 75,570 kW (103,000 hp).
The G95 is a popular choice in the large containerships (9,000 to 21,000 TEU), with 68 sold in the segment since August 2013.
“We attribute the G95’s popularity in this segment to its ability to provide sufficient power for such vessels to reliably achieve their desired operating speed,” says Ole Grøne, Senior Vice President Low-Speed Sales and Promotions, MAN Diesel & Turbo. “Here, the G95’s rpm ensures that a propeller of optimal size can be employed, in turn delivering a low fuel-oil consumption for an optimal fuel economy.
Japan’s Mitsui Engineering & Shipbuilding, another MAN Diesel licensee, completed the world’s first ME-GIE ethane-operated two-stroke diesel engine. The Mitsui-MAN B&W 7G50ME-C9.5-GIE will be installed in the first of three 36,000 m3 liquefied ethane gas carriers being built by Sinopacific Offshore Engineering in China.
MAN Diesel & Turbo reports that ethane was chosen as fuel over HFO because of its competitive pricing as well as the significantly shorter bunkering time it entails. As a fuel, its emissions profile is also better than HFO, as it contains a small amount of sulphur, 15-20 lower CO2 and emits signficantly fewer particles during combustion. The ME-GI engine can also easily be converted to run on methane, if the operator desires.
FEBRUARY 22, 2016—Vard Holdings Limited, one of the major global designers and shipbuilders of offshore and specialized vessels, has secured a new contract valued at NOK 325 million (about $37.7 million) for
Shipping is a crucial contributor to the economies of the Nordic countries—Denmark, Finland, Norway, and Sweden—and the industry continues to be a magnet to attract bright young talent. The region’s ship operators maintain an edge over competitors from lower cost areas by investing in newer tonnage that can be operated efficiently and they are ready to take advantage of every benefit than can be reaped from advances in technology. And, in today’s regulatory climate, it doesn’t hurt that the ecologically conscious Nordic countries are an incubator for green technology.
If we take a look at the numbers of ships controlled from Scandinavia countries published by UNCTAD, the statistics can be misleading. While Finland doesn’t make UNCTAD’s cut of the top 35 shipping nations, the Finnish Shipowners Association says its membership consists of 21 companies operating 101 ships.
What these numbers don’t show is the number of ships chartered in by the region’s shipowners or their strengths in some key sectors. The obvious example of this is Maersk Group. It is the world’s second largest shipowner in terms of its owned fleet (720 vessels totaling 25.5 million gt) but the largest in terms of number of ships controlled (767 vessels totaling 31.7 million gt).
As of the third quarter of last year, the average age of ships in the Norwegian fleet of foreign-going vessels (under Norwegian and other flags) was 10.9 years. Indicating how Norwegians keep the fleet fresh: In the first nine month of last year, 57 newbuildings totaling 2.09 million dwt were added along with 38 pre-owned vessels totaling 818,000 dwt. Equally significantly, disposals and losses totaled 126 ships and 2,.29 million dwt.
The Danish fleet is also young, in gross tonnage terms, 31.9% is under five years old, 28.7% is 5-9 years old, 23% is 10-14 years old, 12.2% is 15-19 years old and just 4.1% is 20 years old or more.
Keeping fleets young means ordering ships. Breaking down 2015 world newbuilding orders by owner’s country of domicile, we find Norway coming in at number 8, ordering 188 vessels totaling 8.7 million dwt and Denmark in the 11th place placing orders for 131 ships totaling 7.2 million tons.
PARTNERING WITH SUPPLIERS
Wherever ships are built—and whoever is buying them—a large percentage of their value is likely to be equipment produced by companies based in the Nordic region, who benefit from a willingness by the region’s shipowners to partner in trialing of equipment aboard ship in real life, working conditions.
Historically, this loop used to also include shipyards, but with the shift of shipbuilding to Asia, this is less the case today. Last year’s Danish Maritime Days included a workshop on “Lack of yard presence in innovation supply chain — How can we as an industry enable improved technology uptake through earlier involvement with the yards?”
Nobody in the room had an instant answer. But there were anecdotal references to the dangers of sharing information too readily with Asian shipyards that see nothing wrong with putting one shipowner’s bright ideas into competitors’ ships.
What remains of the region’s shipbuilding industry is mostly focused on smaller, specialized tonnage, but it retains much of the infrastructure of earlier days including, the intellectual property found in classification societies, design houses, research institutions, model basins and similar facilities—creating ships on the drawing board, the computer and in models that will eventually come to life in full-scale steel in Asia.
Meantime, of course, some yards remain very much in business and winning orders.
DENMARK: MOVING BEYOND
With shipbuilding migrating to lower cost countries, the shipyard capacity in the region has shrunk considerably. For example, there are only a handful of yards in Denmark.
One of those is Fayard A/S in Munkebo. Located on the Odense fjord, it is a large, primarily ship repair, facility whose slogan is “Speed is all—Quality is everything.” It has four large graving docks, all served by high capacity cranes, and a 700 m working berth.
Dry Dock 3, measuring 315/415 m in length and 90 m in width, is the largest dock and is capable of undertaking simultaneous construction work on a variety of ships. Dry docks 1 and 2, may be smaller in size but are 280/303 m lengths and 44/45 m widths and are used for repair and maintenance work on ships. Dry docks 4, measuring 145 m x 30 m x 8 m, is primarily used for smaller vessels. Docks 1, 2 and 4 have modern dock gates and pumping systems that allow the yard to start working on a vessel with 3-4 hours of arrival. The dock gates open or close in just four minutes.
Karstensens Skibsvaerft A/S in Skagen currently has a labor force of around 250, and can build vessels up to 135 m in length. While most are fishing vessels, the yard has been building three Knud Rasmussen-class of offshore patrol vessels, the third of which is near completion using a hull built at Poland’s CRIST shipyard last April.
Orskov Yard A/S in Frederikshavn converts and repairs all types of vessels in facilities that include two graving docks two floating dry docks with a capacity of up to 215 m x 34 m. The yard employs 230 people and cooperates closely with a wide range of subcontractors to provide all-round, one-stop solutions.
Søby Værft AS in Søby Ærø offers ship repair services using three graving docks with capacities up to 115 m x 24 m x 6 m. It also undertakes newbuildings and one project it is getting set for is the EU-supported E-ferry project, aimed at bringing into service a 4.2 mWh battery capacity electrically powered, ICE class B, single ended, drive-through RO/RO passenger ferry with one continuous main deck for trailers and cars. It will use state-of-the-art electric only systems with an automated high power charging system.
The initial aim is to demonstrate an energy efficient and emission free ferry for passengers and vehicles in an operational viable setup on the Soeby-Fynshav and Soeby-Faaborg connections in the Danish part of the Baltic Sea. The longer term aim is to see 10 more E-ferries in operation in Europe and worldwide every year, reaching a total of 100 or more by 2030— saving 100,000-300,000 tonnes of CO2 annually.
SWEDEN: WHERE DID THE YARDS GO?
The Nordic country with the fewest surviving shipyards is Sweden, where the once gigantic industry has shrunk to the point that it apparently no longer supports a national shipbuilding association—so statistics on it are hard to come by.
Newbuilding is pretty much confined to Saab Kockums naval shipbuilding activities and a handful of small yards involved in smaller tonnage.
Two large repair facilities are still operational. Oresund Dry Docks, in Landskrona on the Øresund Strait beween Denmark and Sweden has facilities that include a 195 m x 35 m graving dock and a 165 m x 28 m floating dock. Damen Oskarshamnsvarvet, on the west coast, has facilities that include an 80 m x 15 m floating dock. Activities at Damen Shiprepair Götaverken in Gothenburg ended in 2014, due to “the depressed situation of the Scandinavian shipping market, the increased number of Baltic repair docks and the appreciation of the Swedish Krona (SEK).
Though Gothenburg no longer has a shipyard, it still has one of Europe’s best known towing tanks, operated by SSPA Sweden AB.
SSPA has the capability to perform most kinds of model testing in its facilities: the towing tank, the large cavitation tunnel and the seakeeping and maneuvering basin – Maritime Dynamics Laboratory, (MDL). Wind tunnel tests can be performed at external test facilities.
All test facilities at SSPA are designed for performing tests with large models, which have many advantages as scale effects are reduced and more reliable measurements can be performed.
NORWAY, HANGING IN THERE
For those interested in the preservation of Norwegian shipbuilding capability, a big question in the months ahead will be whether the Vard Group, a Fincantieri company, can continue to keep five Norwegian shipyards alive based on its previously successful strategy of supplying primarily the offshore oil and gas sector with specialized vessels designed and fitted out in Norway using hulls built in Romania.
In addition to its Norwegian yards, Vard has two yards in Romania, two in Brazil and one in Vietnam. Vard’s biggest recent headaches have included well-documented problems with its Brazilian activities and it has said that these are under review.
Outside of Brazil, Vard’s problems are those shared by all shipbuilders historically dependent on the oil and gas sector—getting enough orders to keep capacity occupied and diversifying into other sectors.
Its most recent order came in November and was for design and construction of what was described only as “one offshore vessel for an undisclosed international customer.” It is being designed by Vard Design in Ålesund, Norway. The hull will be constructed at Vard Braila in Romania and outfitting and delivery is scheduled from Vard Langsten in Norway in 2017.
That order followed contracts worth a total $100 million for the design and construction of two offshore subsea construction vessels for Dubai-based Topaz Energy and Marine. The hulls will be constructed at Vard Tulcea in Romania, with delivery scheduled from Vard Brattvaag in Norway.
In the fisheries sector, Vard last year secured an order from Brevik AS of Norway for a coastal fishing vessel, but, for this vessel, Vard Braila in Romania will undertake all stages of production.
Another fisheries order came from a Canadian client and was for a 79 m stern trawler of Rolls-Royce NVC 374 design. Vard Braila will build the hull and the vessel will be fitted out at Vard Aukra in Norway in the fourth quarter of 2016.
Thus far, Vard has either not been looking at the offshore wind sector or has been keeping very quiet about it. That’s not the case with other Norwegian shipbuilders.
A significant current project currently under way at the Ulstein shipyard is the fitting out of the first of two innovative offshore wind industry Service Operation Vessels (SOV) being built for Germany’s Bernhard Schulte Offshore GmbH that will be Ulstein’s first for the offshore wind industry — and the first to feature its innovative X-Stern which allows a vessel to be positioned with the stern faced towards the weather instead of the bow.
The hull of the first X-Stern SOV hull arrived at Ulstein’s Ulsteinvik shipyard in January and is scheduled for sea trials starting late spring. Starting this summer, the vessel will work at the Gemini wind farm in the Netherlands for Siemens Wind Power Service.
A project underway at Fjellstrand AS is another pointer to the growing attraction of offshore wind service opportunities in a depressed oil and gas market. It is converting a platform supply vessel it delivered only in April of last year into a wind farm support vessel.
Havyard Group established its credentials in the offshore wind sector with the delivery last February of the first of three Havyard 803 SOVs to Denmark’s Esvagt. In addition, Havyard has an order from Esvagt for aa design and equipment package for a Havyard 931 CCV crew change vessel that will be built at Spanish shipyard Astilleros Zamakona.
Late last year, Esvagt ordered a further Havyard SOV, aimed at a new niche for vessels of this kind, smaller wind farms. This Havyard 831 design is described as compact and efficient, but with ample capacity to transport service personnel and equipment. The first Havyard 831is also being built outside Norway, at the Cemre shipyard in Turkey.
Though design and equipment deals are obviously profitable for Havyard, that leaves shipyard capacity to be filled and another sector where it has been successful is the design and construction of large fish carriers. Last November Havyard was able to fill a gap in production of these vessels by using the covered building dock at its Leirvik shipyard for refit and refurbishment of two Faroese fishing trawlers.
Kleven, operates two shipyards—Myklebust Verft and Kleven Verft—and its orderbook includes a deep sea minerals exploration vessel and several fisheries vessel in among the AHTs and OCVs.
A recent contract came from Sølvtrans and is for delivery of a live fish carrier vessel for Myklebust Verft. This is Kleven’s second order from Sølvtrans for this type of vessel, both of which are being built to to Rolls-Royce NVC 387 design.
While ship designs are part of the stock in trade at Ulstein, Vard and Havyard, Kleven’s orderbook is pretty much a portfolio for Norwegian specialist ship design firms. The deep sea minerals vessel, which is on order for De Beers Marine Namibia, is being built to MT 6022 design from Marin Teknikk. This design is well proven in the offshore construction segment, but the De Beers ship will include a wide range of tailor made equipment and features.
A large pelagic midwater trawler/ purse seiner that Kleven is building for Gitte Henning AS in Skagen, Denmark, is based on a design from another well known independent design house, Salt Ship Design, which in October had 16 vessels of its design under construction at Norwegian and foreign shipyards.
“Unlike the current offshore market, fisheries and fish farming are doing very well and these segments represents an increasingly important market for Salt,” it said.
In addition to the independent design houses and shipyard design divisions, Norway is also the home of Rolls-Royce’s and Wärtsilä’s Ship Design divisions, which have absorbed various independents over the years. Having a ship design department makes all sorts of sense for both of them, as a ship design is the envelope for, quite literally, a boatload of equipment and systems.
FINLAND, BACK FROM THE BRINK?
In Finland, thanks largely to government support —including diplomatic efforts— a large part of the shipbuilding industry has emerged from the ashes of what was STX Finland.
Most importantly, with a lot of Finnish Government coaxing, Germany’s Meyer Werft has acquired the Turku shipyard, enabling it to continue as one of the world’s premier cruise ship yards.
Shipbuilding has also returned to the Rauma shipyard after STX announced its closure in 2013, with the site being sold to the local municipality. The shipyard reopened as Rauma Marine Constructions Oy (RMC) the following year and in December 2015 reported that it was to “receive a major infusion of capital for further growth from the government backed Finnish Industry Investment Ltd, and two investment companies, Finda and a fund managed by Taaleritehdas. That news came the day after the Finnish Ministry of Defense issued a Request For Information to kick off a long planned plan to build four new corvette size vessels.
The Rauma shipyard also has considerable expertise in the area of icebreaking vessels — which keeps what is now Arctech Helsinki Shipyard from having a monopoly in that area. When STX Finland ’s troubles threatened the survival of the Helsinki yard, Russia’s United Shipbuilding Company took a 50% stake in and subsequently took total ownership control and the yard’s orderbook primarily includes advanced icebreaking tonnage for Russian projects, though an icebreaker for the Finnish Transportation Authority is currently fitting out.
The other repository of Finnish icebreaking knowhow is ice-going vessel design and engineering specialist Aker Arctic, whose capabilities include ice model testing. Its largest shareholder is Finnish Industry Investment, which is also major stakeholder in the reborn Rauma yard.
APRIL 2, 2013 — A project that started with an anonymous request to Norwegian ship designer Marin Teknikk has resulted in shipbuilder Kleven winning a contract from the still undisclosed owner to