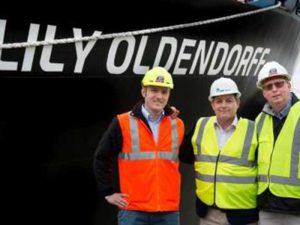
Oldendorff drives digital revolution with BMT
APRIL 3, 2017 — Lübeck, Germany, headquartered bulker specialist Oldendorff Carriers and BMT Group subsidiary BMT SMART have reached a new agreement that has led to the roll out of fleet performance
APRIL 3, 2017 — Lübeck, Germany, headquartered bulker specialist Oldendorff Carriers and BMT Group subsidiary BMT SMART have reached a new agreement that has led to the roll out of fleet performance
FEBRUARY 9, 2017 — DNV GL is launching a new marine industry data platform – “Veracity” – to help the industry improve its profitability and explore new business models through digitalization. “The
SEPTEMBER 26, 2016 — Xeneta, a benchmarking and market intelligence platform for containerized ocean freight, is looking to bring a new understanding to the world’s biggest container shipping market by opening its
SEPTEMBER 14, 2016 — BAE Systems is leading a consortium of technology suppliers to develop software that monitors the equipment, fuel and energy performance of a ship. Known as Ship Energy Assessment
SEPTEMBER 11, 2016—Unlocking big data is a key to making shipping more efficient. But securing that data is also critical. With most of the equipment and systems on board a ship networked,
Rapid advances in the development of information and communication technologies now make it possible to collect large volumes of data on a diverse range of items related to ship operations. However, the approach to data capture is still very fragmented with similar data being sent to several vendors and analysis still being carried out almost entirely on a ship-by-ship basis.
To make larger gains, an effective platform capable of centralizing and managing such diverse data is essential. However, creating and maintaining this kind of platform is costly, time-consuming and unrealistic for many organizations.
Special care also needs to be given to the handling of data to ensure confidentiality of information; hence it is also necessary to establish a secure yet effective platform from an impartial perspective.
As an independent, non-profit organization with over a century of experience in ship classification, ClassNK has drawn on its extensive technical knowledge and expertise to develop Ship Data Center Co., Ltd.
The Data Center consists of a secured shipping operations database which will serve as an information hub to independently manage the utilization of big data in the maritime industry. Through the center’s integrated data, the industry can maximize the benefits of big data with a minimum cost and burden.Trials of the Data Center will commence on a container vessel in February 2016 in cooperation with a Japanese shipping company. Various information including data from the ship’s voyage data recorder and data logger will be gathered from the vessel.
Full operation of the Data Center is scheduled from April 2016.
ClassNK sees opportunities for future application of the Data Center as “infinite.”In addition to optimizing ship operations and improving condition-based monitoring of machinery, the Data Center could also be used to help the industry overcome current and emerging challenges.
For example, the entry into force of the Monitoring, Reporting and Verification (MRV) regulation by the EU requires shipowners and operators to annually monitor, report and verify fuel consumption for vessels 5,000 gt or over which call at any EU port. Data collection will be required from January 1, 2018. The Data Center plans to offer shipowners and operators a secure and neutral database in which to store and manage these vast amounts of fuel consumption data.
ClassNK says that establishment of Ship Data Center Co., Ltd. reinforces its position as part of indispensable infrastructure of the industry and demonstrates its commitment to creating a safer, greener and more efficient global maritime industry.
Yet, the requirements and demands put upon naval architects and shipyards can sometimes feel worlds away from the day-to-day operation of vessels. The challenge of crews having different priorities and needs from their shore-based counterparts has also been well documented. So what can be done to draw these different groups together?
Years of experience in providing both ship design software to yards and onboard performance monitoring solutions that report in real-time to shore based offices, gives NAPA an interesting umbrella perspective. We have seen how sometimes the day-to-day demands on each of these industry segments, and regulations they are working to, can pull them each in different directions. But we can also see that, on the whole, their end goal is fundamentally the same – safe, efficient and productive vessels that serve both their owner and the wider supply chain.
Increasing visibility and understanding between each of these vital functions and helping each to understand their own contribution to the whole, and how it impacts and relates to work in other sectors, will be increasingly vital as the industry evolves technologically and comes under greater environmental scrutiny. With the advent of big data, better tools to analyze it and improved systems to share it, this is quickly becoming more feasible.
Yards face increasing regulatory pressures that require internal validation as well as increased communication and data sharing with class societies. Tools and data interfaces are rapidly developing to make this a streamlined part of the vessel design process and deliver an easy shift from design terminals to construction plans for yards. But, by far the most interesting progress that data can help deliver is designing for real-world vessel performance. Until recently, yards designed vessels to meet the required sea-trial performance parameters – and sea-trial data confirming whether or not that aim was achieved was the only performance information they were provided with.
However, sea trial conditions rarely reflect those faced during real-world vessel transits and expected performance often doesn’t match with real experiences. Until now, that real world information never got back to the yard. The sea trial data was all they had to go on, so they were never able to identify these anomalies and correct them to deliver high-performance vessels for real conditions.
Performance monitoring tools have been in use for many years to collect this data for ship owners and operators. With an added layer of analysis it is now turned it into usable information for both shore-based offices and vessel crews to manage vessels in real time. More advanced performance monitoring and optimization tools like ClassNK-NAPA GREEN provide further big data analytics, combining weather, speed positioning and route data with measured vessel data to enable a true view of efficiency. It presents users with actionable information about each vessel and the fleet as a whole.
Our question was: Why could access to this data not be extended to the yard that designed and built the vessel? This is one of the things we have been trialling as we enhance and continue to build on the success of ClassNK-NAPA GREEN. With agreement from all parties, designers are being given access to efficiency data from the ships that are now in operation. This joined up approach to data sharing will help to drive the entire industry towards common goals.
That is just one example of how big data can change the way we work and how greater transparency could open up pathways for improvement across the industry. But big data—in fact any data—is only relevant when it responds to a businesses specific needs. This business intelligence can be anything a business needs to know to improve or develop its operations, but ultimately you can’t manage what you don’t measure.
Stena Line’s Energy Saving Program (ESP) has excellently demonstrated this ongoing management. Since 2005, it has been adjusting vessel operations as well as testing other efficiency solutions using data analytics to evaluate fuel-saving effectiveness and ROI. In that time Stena has adopted changes ranging from bulbous-bow removal to energy-conserving window films. With ClassNK-NAPA GREEN installed on 24 vessels for day-to-day performance optimization, the ESP has resulted in $17 million in savings to date.
Equally, even with measurement in place, sometimes it can be difficult to know what to manage if you don’t ask the right questions. That’s where ongoing storage for historical big data analysis can be incredibly beneficial. For example, one major cruise line had been collecting data with onboard performance management and optimization systems since 2006 but it was only fairly recently that they wanted to ascertain the cost-benefit relationship of waiting for late passengers.
After analysis on the waiting time and period of increased speed to the next destination held in the existing data it was discovered that the current policies were costing tens of millions of dollars every year. This resulted in a policy change across the cruise line’s business.
Sometimes it’s a combination of the two that results in the greatest benefit. Real-time measurement of current performance when compared against data benchmarks of normal vessel operation allows easy identification of underperforming systems. For example, after minutes reviewing the real-time analytics for a container vessel, Class NK-NAPA Green identified that the hull needed cleaning. Once actioned, this cleaning reduced the vessel’s monthly fuel expenditure by $60,000.
The common element to each of these examples and ways of working is big data and a willingness to share that data to reach a common goal. Whether it’s to give yards the knowledge they need to design for real-world efficiency or simply to manage vessel maintenance, effective implementation of the right questions and powerful tools that can help you answer them can have a real impact. Applied wisely, transparently and collectively, big data can better connect us and support us all in delivering a more productive, efficient and safer future for shipping.