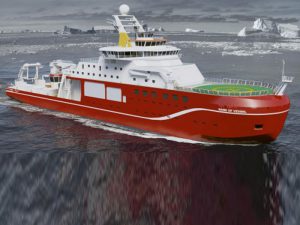
Cammell Laird to build $307 million polar research ship
The decision follows a 12-month competitive tender process that involved bids from shipyards in the U.K., Spain, Norway, Singapore and South Korea.
The Birkenhead shipyard is expected to cut steel in autumn 2016 and deliver the next generation polar research vessel ready for operation by 2019.
Cammell Laird Chief Executive John Syvret said: “The new contract, which will be finalized later this year, is expected to secure 400 jobs at Cammell Laird and a further 100 jobs within the local supply chain. Cammell Laird has a very successful apprenticeship scheme and would plan to recruit 60 apprentices throughout the term of the contract. Being selected as the preferred bidder in a global tender to undertake such an exciting and major infrastructure project is fantastic news for our workforce, the local region and the U.K. We look forward to helping the U.K. explore the depths of the ocean and push the boundaries of U.K. science.”
The new polar research ship, which will operate in both Antarctica and the Arctic, will be able to endure up to 60 days in sea-ice to enable scientists to gather more observations and data.
It is expected to have ice-breaking capabilities that will allow it to break ice up to one meter thick when traveling at 3 knots and will be able to accommodate up to 60 researchers and technical support staff.
The ship will be the first British-built polar research vessel with a heli-deck to open up new locations for science and will be one of the most sophisticated floating research laboratories operating in the Polar Regions.
Funding for the new polar research ship was announced in April 2014 as part of the U.K. Government’s science capital program.
Cammell Laird has been selected by the Natural Environment Research Council (NERC) through a full competitive procurement process.
NERC Chief Executive Professor Duncan Wingham said: “This new research ship, which is expected to become operational in 2019, will be equipped with onboard laboratory facilities and will be capable of deploying robotic technologies to monitor environmental changes to the polar oceans and will help U.K. scientists continue to lead the world in understanding our polar regions.
“Changes in both the Antarctic and Artic marine ecosystems affect the U.K.’s environment and economy, particularly in industries such as fishing and tourism. The Natural Environment Research Council funds polar research so that as a nation, we can develop policies to adapt to, mitigate or live with environmental change.
“This new polar ship will be a platform for a broad range of science, researching subjects from oceanography and marine ecology to geophysics.”
The new ice-strengthened ship will be operated by British Antarctic Survey (BAS), on behalf of NERC.