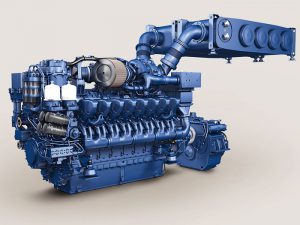
MTU to showcase green and hi-tech at SMM
JULY 19, 2016 — Rolls-Royce will be presenting new MTU brand propulsion systems designed to meet IMO III and EPA Tier 4 emission regulations for commercial, offshore and military vessels and yachts
JULY 19, 2016 — Rolls-Royce will be presenting new MTU brand propulsion systems designed to meet IMO III and EPA Tier 4 emission regulations for commercial, offshore and military vessels and yachts
The certificates cover key components of the system, including the complete dosing and control system, injectors, load sensors and the human machine interface (HMI) remote monitor, as well as catalyst and reactor hardware configurations for IMO Tier III applications.
“We’re pleased to receive this important classification. Tenneco’s high horsepower SCR technology is designed to meet IMO Tier III NOx reduction requirements that take effect in 2016 and this classification further demonstrates our readiness to deliver these solutions for ships or vessels anywhere in the world,” said Jay Kedia, Tenneco managing director, large engine.
Tenneco’s SCR aftertreatment system features a complete dosing control solution specifically designed for marine engine applications up to 7,500 kW or 10,000 hp. The system is designed to enable propulsion and auxiliary engines to meet U.S. EPA Tier 4 and IMO Tier III regulatory requirements and provide precise and reliable delivery of liquid urea via a proprietary, high-performance injector design, a precision mechatronic fluid delivery pump and customizable remote monitoring and controls.
In the past year, the company has conducted a series of validation tests to demonstrate how the system’s form, fit, function and performance capabilities can be easily integrated into a vessel’s engine and control architecture.
Most recently, through a partnership with the Texas A&M Maritime Academy, Tenneco conducted saltwater sea trials onboard the TS General Rudder in the Gulf of Mexico. Tenneco’s SCR system was installed on a 33-year old 800 horsepower, Tier 0 engine that was operational for the duration of the Academy’s summer cruise training period. Results demonstrated NOx reduction levels that kept the General Rudder compliant with today’s stringent U.S. EPA Tier 4 marine emission requirements under all operational conditions.
Tenneco conducted similar tests on a 224 ft\ training vessel in the Great Lakes in 2014. In a series of validation tests, including the ISO 8178 E2 cycle, when a similar engine was outfitted with Tenneco’s SCR system, the engine met all criteria for IMO Tier III, including NOx.
In addition to DNV GL classification, Tenneco’s high horsepower SCR system has been awarded product design classification from ABS, and is designed to meet the requirements of other major maritime classification societies including CCS, KR and Class NK.
SCR System Features
The SCR system’s modular design enables seamless integration for a broad range of engine sizes and works with electrically or mechanically controlled engines. It has been validated for durability and all components are easy to maintain and service without the need for special tools.
The fluid delivery system with dosing control software is capable of managing multiple injection points and sensors. The system can support urea flows up to 120 meters, which enables a wide array of installation options. Airless urea injection provides high dosing accuracy and consistency without the need for dedicated compressed air.
The system’s Human Machine Interface (HMI) can be accessed on the front of the fluid delivery box or remotely via a touch screen tablet. It features an easy-to-use interface to monitor and control all system parameters including but not limited to NOx reduction performance and urea concentration levels in real time. Onboard diagnostics are capable of monitoring more than 100 parameters including urea leakage, sensor faults and backpressure.
For many shipowners, it could make EGR —rather than SCR (selective catalytic reduction) — the optimum means of meeting the NOX reduction requirements set by EPA Tier 4 and IMO Tier III requirements.
Developed by Alfa Laval in close cooperation with MAN Diesel & Turbo, the Aalborg EGR-HPE is a revolutionary new economizer enclosed in a pressure casing. Placed in-line ahead of the pre-scrubber sprayers in the EGR circuit, it can be used to gain a number of advantages. If connected to a conventional waste heat recovery system, for example, waste heat recovery becomes substantially more efficient – and is possible at significantly lower engine loads.
“EGR provides Tier III NOx compliance with a very compact footprint, but compliance itself is only part of the full potential,” says John Pedersen, Business Manager, Boilers, Combustion & Heaters at Alfa Laval. “Working closely with MAN Diesel & Turbo to optimize the EGR technology, we saw additional opportunities through our expertise in marine boilers. The result is the Alfa Laval Aalborg EGR-HPE economizer, which paves the way for extraordinary energy and fuel savings.”
“By moving the break point for waste heat recovery from a medium engine load down to a low load, the Aalborg EGR-HPE enables even slower steaming,” says Mr. Pedersen. “That means fuel savings that quickly pay back the economizer, offset the EGR investment and lower CO2 emissions on top of the NOx reduction.”
The source of all these benefits: the heat that would otherwise be lost during EGR. In the EGR process, around 30% of the exhaust gas is directed back into the engine, reducing the combustion temperature and thus the production of NOx. However, as only the 70% of the gas now reaches the traditional exhaust gas boiler after the turbocharger, waste heat recovery is reduced by 30%.
However, the Aalborg EGR-HPE is placed in-line before the EGR pre-scrubber spray jets that cool the exhaust gas. The economizer thus has access to much higher temperatures than traditional exhaust gas boilers. So, while the installation is light, compact and self-cleaning due to the high speed of gas flow, its application potential is enormous. This can be seen in the way it increases the efficiency of a conventional waste heat recovery system.
The Aalborg EGR-HPE is integrated with conventional waste heat recovery after the turbocharger by means of its steam drum, which is shared by the traditional exhaust gas boiler. With the output of the traditional economizer feeding into the shared drum, the Aalborg EGR-HPE produces extremely high-quality steam with a temperature of just above 400°C, bringing the waste heat recovery system to a much higher level of efficiency.
“The difference in steam quality has a direct effect on the performance of the steam turbine,” says Mr. Pedersen. “Installation factors play a role, but a substantial increase in power generation can be expected.”
Fuel savings through even slower steaming
Even more importantly, using the Aalborg EGR-HPE in an integrated system allows waste heat recovery to occur at lower main engine loads than possible with a traditional waste heat recovery system in Tier III operation. In other words, it creates the possibility for even slower steaming.
“The EGR economizer makes waste heat recovery beneficial at far lower engine loads, down to around 30%” says Mr. Pedersen. “This means that vessels can steam even slower, with huge fuel savings as a result. A vessel performing EGR and using the Aalborg EGR-HPE will be not only compliant with Tier III, but also substantially more fuel efficient.”
Proven results at sea
The savings with the Aalborg EGR-HPE are not merely theoretical.
In a project supported by the Danish Energy-Technological Development and Demonstration Program (EUDP) and developed in cooperation with Aalborg University, the EGR boiler has been rigorously tested aboard the Maersk Cardiff, a 4,500 TEU containership delivered to Maersk Line in 2013.
“As a front-runner in the pursuit of green technologies, we were keen to see what the Aalborg EGR-HPE could do,” says Ole Christensen, Senior Machinery Specialist at A.P. Moller-Maersk. “But while we were enthusiastic about the boiler’s potential, we were also somewhat uncertain as how it would handle the physical realities of EGR. The temperatures are twice as high as those of traditional waste heat recovery, and the gas pressures are far greater.”
Those concerns disappeared when the boiler was brought online with the Maersk Cardiff’s two-stroke MAN B&W 6S80ME-C9 engine in November 2014. “Not only did the boiler survive,” says Mr. Christensen, “the results we have seen during testing are very promising.”
“By introducing the EGR boiler into the NOx equation, we’ve truly changed the balance,” says Alfa Laval’s Pedersen. “Suddenly EGR is not only a means of Tier III compliance, but also a means of radically improving the vessel’s energy efficiency. And that makes it a very different sort of investment.”
The HiMSEN engine has just passed another milestone. The next generation CLEAN (Customer, Liability, Environment, Acceptable Technology, No Defect) HiMSEN engine has now completed type approval testing in the presence of eight major classification societies including ABS, DNV/GL, LR and KR.
The four-stroke CLEAN HiMSEN engine (Model H21C) improves power output by 20 percent and fuel efficiency up to 2 percent compared to the existing same class four-stroke engines, H21/32, while physical size and weight are 10 percent lower, thanks to the utilization of high pressure combustion technology.
The IMO Tier III-compliant engine emits 98 percent less NOx with the use of HHI’s proprietary Hyundai Selective Catalytic Reduction technology, NoNOx.
Mr. Youn Joong-geun, executive vice president of HHI’s Engine & Machinery Division said, “Our next-generation CLEAN HiMSEN engine is the culmination of our 40 years of technological know-hows and experiences. With the customer-oriented engineering, the high-output and high-efficiency engine will surely bring mutual benefits to HHI and its valued customers.”
OCTOBER 2, 2014 — Fuel injection specialist L’Orange has introduced L’Onox: a new product for exhaust after-treatment to enable engine manufacturers to meet the restrictions on NOX emissions mandated by IMO Tier
SEPTEMBER 9, 2014 — MAN Diesel & Turbo used this year’s SMM event in Hamburg to present the MAN 12V175D. The twelve-cylinder model, developed especially for use in the shipping industry, is
SEPTEMBER 8, 2014 — Rolls-Royce Power Systems AG says that its MTU brand and Fairplay Towage are to test an MTU diesel genset with SCR exhaust after treatment in a harbor tug