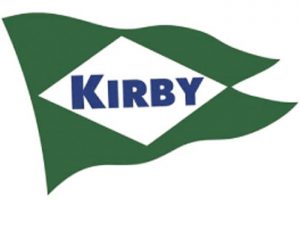
Kirby reports third quarter results
Consolidated revenues for the 2015 third quarter were $532.6 million compared with $680.7 million for the 2014 third quarter.
President and CEO David Grzebinski said the results were “largely in line with our expectations.”
“Demand across the majority of the products we carry in the inland marine transportation market remained stable with utilization in the 90% to 95% range,” he said. “Market pressure from inland tank barges shifting out of crude oil service led to continued modest pressure on contract renewal pricing. Spot prices were generally around contract price levels throughout the quarter. In the coastal marine transportation market, pricing for term contract renewals increased modestly. Our results also reflected the anticipated earnings impact from heavy coastal equipment shipyard activity.”
Mr. Grzebinski called market conditions in Kirby’s land-based diesel engine services business, as continuing to be challenging due to the decline in the price of crude oil and, consequently, the low utilization levels of the oilfield service industry pressure pumping fleet.
In the marine diesel engine services and power generation markets, results reflect continuing soft activity in the Gulf of Mexico oilfield service market, but otherwise stable levels of demand.
MARINE TRANSPORTATION
Marine transportation revenues for the 2015 third quarter were $418.3 million compared with $448.7 million for the 2014 third quarter. Operating income for the 2015 third quarter was $93.7 million compared with $112.1 million for the 2014 third quarter.
Kirby’s inland marine transportation business maintained tank barge utilization in the 90% to 95% range.
Demand for inland barge transportation of petrochemicals, refined products and black oil products, excluding crude oil, was consistent with the second quarter. Demand for barges moving crude oil and condensate during the quarter was lower both sequentially and year over year.
Operating conditions were challenging due to scheduled lock closures along the Gulf Intracoastal Waterway and high water conditions during the first part of the third quarter. Delays related to lock outages contributed to a 40% increase in delay days relative to the prior year quarter and a decline in ton miles. In addition to increased delay days, fuel prices, which were down 38% year-over-year, contributed to the year over year decline in revenue.
Demand in the coastal marine transportation market for the transportation of refined petroleum products, black oil, and petrochemicals was relatively stable, although demand for equipment for crude oil transportation declined sequentially and year over year.
Coastal fleet utilization remained in the 90% to 95% range and operating conditions were seasonally normal during the third quarter. A continued heavy shipyard schedule impacted operating results.
The marine transportation segment’s 2015 third quarter operating margin was 22.4% compared with 25.0% for the third quarter of 2014 as a result of higher labor costs, including pension, lower inland marine transportation rates, increased shipyard activity and higher depreciation expense in the coastal business, and the impact of fuel price escalators on inland marine affreightment contracts.
CASH FLOW
Kirby continued to generate strong cash flow during the 2015 first nine months with EBITDA of $437.5 million compared with $484.6 million for the 2014 first nine months. Operating cash flow was used in part to fund capital expenditures of $265.2 million for the 2015 first nine months, including $66.6 million for new inland tank barge and towboat construction, $75.2 million for progress payments on the construction of four new coastal articulated tank barge and tugboat units (“ATBs”), $3.4 million for progress payments on the construction of two 4900 horsepower coastal tugboats, $1.6 million for progress payments on the construction of a new coastal petrochemical barge and $118.4 million primarily for upgrades to existing inland and coastal fleets.
Additionally, Kirby spent $41.3 million to acquire six pressure barges in the first quarter and a total of $202.2 million on share repurchases in the first nine months of 2015.
Total debt as of September 30, 2015 was $810.4 million versus $716.7 million on December 31, 2014, and Kirby’s debt-to-capitalization ratio was 26.4%.
OUTLOOK
Mr. Grzebinski said, “Our earnings guidance range for the 2015 fourth quarter is $0.93 to $1.03 per share and we are revising our full year 2015 guidance range to $4.10 to $4.20 per share [down from the prior guidance of $4.10 to $4.35 per share]. In our inland marine transportation market, our fourth quarter outlook reflects continued modest pricing pressure. Utilization in Kirby’s inland fleet, however, is projected to remain in the 90% to 95% range. In our coastal marine transportation market, although we’ve seen some industry spot availability related to the uncertainty around crude supplies, we expect supply and demand to remain consistent with the first nine months of the year and Kirby’s fleet utilization to remain above 90%. Our guidance assumes normal fourth quarter operating conditions for both the inland and coastal marine transportation markets, including the winter cessation of most operations in Alaska.”
Mr. Grzebinski said demand is expected to remain weak in the land-based diesel engine services market and the offshore oil services portion of the marine diesel engine services market, but is expected to remain relatively stable in the marine and power generation markets.
CAPITAL SPENDING
Kirby expects 2015 capital spending to be in the $320 to $330 million range, an increase of $5 million from earlier capital spending guidance. Contributing to this is a shipbuilding contract entered into the quarter for a 35,000 barrel coastal petrochemical tank barge. The vessel will enter service under contract with an existing customer on delivery, expected in early 2017.
The capital spending guidance range includes approximately $70 million for the construction of 38 inland tank barges and three inland towboats, all expected to be delivered in 2015.The capital spending guidance range also includes approximately $100 million in progress payments on new coastal equipment, including two 185,000 barrel coastal ATBs, two 155,000 barrel coastal ATBs, two 4900 horsepower coastal tugboats and the new coastal petrochemical tank barge.The balance of $150 to $160 million is primarily for capital upgrades and improvements to existing inland and coastal marine equipment and facilities, as well as diesel engine services facilities.